Cuando se diseñan bicicletas de carga para uso comercial a largo plazo -ya sea para reparto de alimentos, servicios postales o logística-, el coste de mantenimiento es uno de los factores más críticos que influyen en el coste total de propiedad (TCO). En Regenhemos visto de primera mano cómo selección de piezas modulares puede transformar la capacidad de servicio, el tiempo de actividad y la economía de las reparaciones.
Este artículo explica en profundidad cómo el diseño modular reduce los costes de mantenimiento de las bicicletas de carga y ofrece ejemplos reales de nuestro proceso de desarrollo.
¿Qué es la selección de piezas de diseño modular de Cargo Bike?
Selección modular de piezas es la práctica de diseñar un producto (en este caso, una bicicleta de carga) con componentes intercambiables que pueden instalarse, sustituirse o mejorarse de forma independiente sin afectar al resto del sistema.
A diferencia de los diseños monolíticos o integrados a medida, los sistemas modulares permiten:
- Fácil desmontaje y montaje
- Intercambiabilidad de piezas entre modelos
- Diagnóstico y solución de problemas simplificados
- Gestión racionalizada del inventario
La modularidad está muy extendida en la automoción, la industria aeroespacial y la electrónica, y las bicicletas de carga se están poniendo al día rápidamente.
Componentes clave de las bicicletas de carga adaptados a la modularidad
Los siguientes componentes son especialmente adecuados para la arquitectura modular de las bicicletas de carga:
Componente | Característica modular recomendada |
Batería | Conector estandarizado, desmontable, para montaje en rack trasero/tubo descendente |
Motor | Unidad central o hub intercambiable con controlador externo |
Caja de carga | Chasis deslizante o atornillado, interfaz de bastidor estándar |
Sistema de iluminación | Unidades LED enchufables con cables de conexión rápida |
Sistema de frenado | Pinzas universales, de montaje posterior mecánico o hidráulico |
Manillar Cockpit | Pantalla extraíble, acelerador, palancas de freno con liberación rápida del cable |
Módulo IoT/GPS | Interfaz externa, impermeable, a prueba de manipulaciones, USB o CAN-Bus |
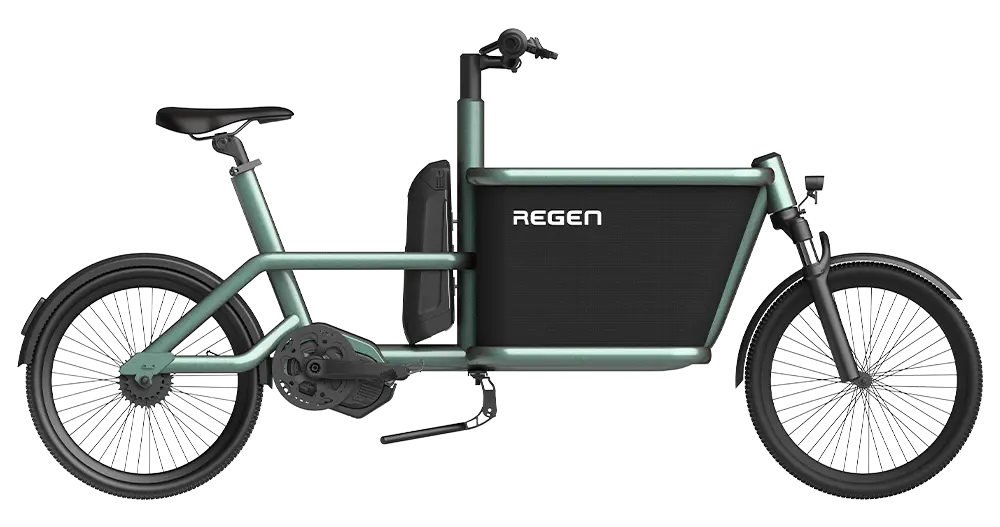
Bicicleta de carga eléctrica Regen 02
¿Busca una lavadora de carga frontal compacta y personalizable para su marca?
Probado por TÜV en proyectos personalizados anteriores. Modelo disponible públicamente: configurable, probado y listo para escalar.
Cómo el diseño modular reduce los costes de mantenimiento
1. Reparaciones más rápidas = menor coste de mano de obra
Gracias a las piezas modulares, los mecánicos pueden aislar las averías y sustituir las piezas sin desmontaje completo del sistema. Así se reducen las horas de trabajo y se reducen los costes.
Por ejemplo:
- Luz trasera LED defectuosa puede desenchufarse y sustituirse en 2 minutos, en lugar de recablear a través del cuadro.
- Motores de tracción central con soportes de montaje rápido (por ejemplo, Bosch Cargo Line) permiten cambiarlos sin desmontar la transmisión.
Esto es especialmente valioso para los operadores de flotas, donde el tiempo fuera de la carretera equivale a pérdida de ingresos.
2. Los recambios estandarizados reducen los costes de inventario
Si su línea de bicicletas de carga utiliza frenos, baterías, pantallas y neumáticos comunespuedes:
- Compre repuestos al por mayor a menor coste.
- Minimice la complejidad de las SKU del almacén.
- Comparta componentes entre familias de productos.
Ejemplo: Utilización de Neumáticos 20×2,125" CST o Schwalbe en todas las ruedas delanteras significa que sólo necesita almacenar un tamaño para el mantenimiento, lo que reduce los costes de inventario hasta en 30%.
3. Ciclo de vida más largo gracias a la posibilidad de actualización
El diseño modular hace que sus bicicletas preparado para el futuro:
- Aumento de la capacidad de la batería (por ejemplo, de 500 a 750 Wh)
- Cambie las pantallas por una nueva versión compatible con IoT
- Instale mejores frenos a medida que aumente la carga de uso
En lugar de sustituir toda la moto, usted prolongar su vida útil con mejoras graduales, reduciendo tanto los costes de capital como los de mantenimiento.
4. Formación y asistencia simplificadas
Para fabricantes de equipos originales o gestores de flotas con mecánicos internos, los diseños modulares simplifican la formación técnica:
- Los técnicos aprenden un sistema de baterías, un protocolo de frenado, una arquitectura de controlador
- Las herramientas de diagnóstico pueden reutilizarse en todos los modelos
- Los manuales de servicio siguen siendo coherentes
Esto evita costosos errores y reduce la necesidad de subcontratar reparaciones especializadas.
5. Menor riesgo de garantía y mejor control de daños
En situaciones de entrega, las bicicletas de carga pueden sufrir impactos o quedar expuestas. Con componentes modulares:
- Una caja de carga agrietada no significa sustituir todo el bastidor
- Los cables dañados pueden intercambiarse mediante arneses enchufables
- Los mecanismos de dirección pueden sustituirse independientemente de la horquilla delantera
Esto aísla los problemas y evita que pequeños fallos se conviertan en grandes costes de reparación.
Ejemplos reales de diseño modular de Regen en los proyectos anteriores
En Regen, aplicamos la modularidad tanto en el diseño del bastidor como en la integración de componentes como:
Cajas de carga extraíbles (con diseño personalizado disponible)
Nuestras cajas de carga se fijan mediante Soportes de 4 puntos que permiten a los usuarios cambiar de una a otra:
- Cajas logísticas de 400L
- Cajas isotérmicas para alimentos de 700L
- Cajas promocionales de marca con tapa
El cambio de cajas se realiza en menos de 10 minutos, lo que resulta ideal para los operadores de flotas que prestan servicio a múltiples sectores.
Sistemas eléctricos normalizados
Nosotros usamos un caja de conexiones central con conectores estancos (IP67) para:
- Controlador del motor
- Batería
- Sistema de iluminación
- Módulo GPS
Más información: Configuración funcional de ODM
Horquilla delantera y dirección Plug-and-Play
Para las bicicletas Long John, nuestro varillaje de dirección modular significa que si la horquilla o la barra de dirección delantera están dañadas, pueden desmontarse con herramientas básicas y sustituirse sin necesidad de realinear toda la moto.
Impacto en los costes: En cifras
Categoría de costes | Sin modularidad | Con modularidad | Reducción (%) |
---|---|---|---|
Mano de obra media de reparación por bicicleta/año | €200 | €120 | ↓40% |
Coste del inventario de piezas de recambio (10 SKU) | €1,500 | €900 | ↓40% |
Tiempo medio de inactividad por reparación (días) | 4 | 1.5 | ↓63% |
Coste total anual de mantenimiento por cada 100 bicicletas | €25,000 | €15,000 | ↓40% |
Recomendaciones para diseñadores y operadores de flotas
Para diseñadores de bicicletas de carga (OEM):
- Usar soportes universales (por ejemplo, frenos post-mount, bujes con puntera de 100 mm)
- Elija componentes estándar cuando sea posible (Shimano, Bafang, etc.)
- Diseño de mazos de cables con códigos de color y conectores codificados
Para operadores de flotas:
- Formar a los técnicos de campo en el diagnóstico y la sustitución de módulos
- Estandarice su flota en todos los modelos con piezas compartidas
- Construir un kit de piezas modulares por región
Lista de referencias
- Shimano Europa. (2023). Guía técnica: Compatibilidad de frenos MTB y de carga.
- Sistemas eBike de Bosch. (2024). Guía de servicios de Cargo Line.
- Comité Europeo de Normalización (CEN). (2022). EN 17860: Bicicletas de carga - Requisitos de seguridad y prestaciones.
- Agencia Internacional de la Energía (AIE) (2023). Informe sobre micromovilidad y logística urbana.
- Teltonika Telemática. (2023). Integración de dispositivos GPS en aplicaciones de carga.
- CargoFacts. (2023). Coste de propiedad de las flotas urbanas de transporte electrónico de mercancías.
- Regen documentación técnica interna e informes de opinión de los clientes (2024-2025).
Reflexiones finales
Reducir los costes de mantenimiento no consiste sólo en utilizar piezas mejores, sino también en diseñar con inteligencia desde el principio. Las bicicletas de carga modulares ofrecen a los fabricantes y a los operadores de flotas una plataforma preparada para el futuro, escalable y de fácil mantenimiento. En Regen, seguimos integrando la modularidad en cada nuevo modelo que lanzamos porque sabemos que mantiene las bicicletas en la carretera y las empresas en funcionamiento.
¿Busca una solución modular de bicicletas de carga para su flota? Contáctanos para saber cómo podemos ayudarle en su próxima implantación con diseños personalizables y de bajo mantenimiento.