Introduction : Répondre aux exigences des vélos électriques modernes
Les vélos électriques et les vélos cargo révolutionnent le transport urbain et devraient connaître une croissance rapide en Europe.d'un marché estimé à 1,05 milliard USD en 2024 à environ 1,60 milliard USD en 2029 Ces vélos transportent de lourdes charges dans les rues de la ville par tous les temps, et les cyclistes s'attendent à ce qu'ils soient durable, fiable et durable. À Regen TechNous avons constaté comment des conditions difficiles comme la pluie, le sel de voirie et une utilisation constante peuvent mettre les cadres de vélo à rude épreuve. Dans cet article, nous expliquons pourquoi. Revêtement par dépôt électrophorétique (ED) est devenu notre solution de référence pour la protection des cadres de vélos électriques et cargos. Nous détaillerons le procédé de revêtement ED, le comparerons au revêtement en poudre traditionnel et à la peinture liquide, et montrerons les avantages du revêtement ED pour tous, des passionnés de vélo aux ingénieurs, en passant par les commerçants et les responsables de marque.
À la fin, vous comprendrez comment fonctionne le revêtement ED (également connu sous le nom de revêtement électronique (ou peinture électrophorétique) confère aux cadres de vélo une résistance à la corrosion et une durabilité dignes de l'automobile. Sur un ton clair et pédagogique, Regen Tech vous guidera à travers cette technologie et ses avantages concrets pour les vélos qui doivent résister aux rigueurs de la logistique urbaine quotidienne.
Qu'est-ce que le revêtement électrophorétique ? Le procédé expliqué
Le revêtement ED est un procédé de peinture très avancé qui utilise l'électricité pour déposer une couche de peinture très uniforme sur une surface métallique. En termes simples, nous plongeons le cadre du vélo (métallique et conducteur) dans un réservoir de peinture liquide et appliquons un champ électrique. Les particules de peinture dans le liquide sont chargées et émigrer sur le châssis, formant une fine couche uniforme sur toutes les surfaces. Cette technique est identique à celle utilisée pour l'apprêt des carrosseries automobiles, réputé pour son exceptionnelle protection contre la corrosion.
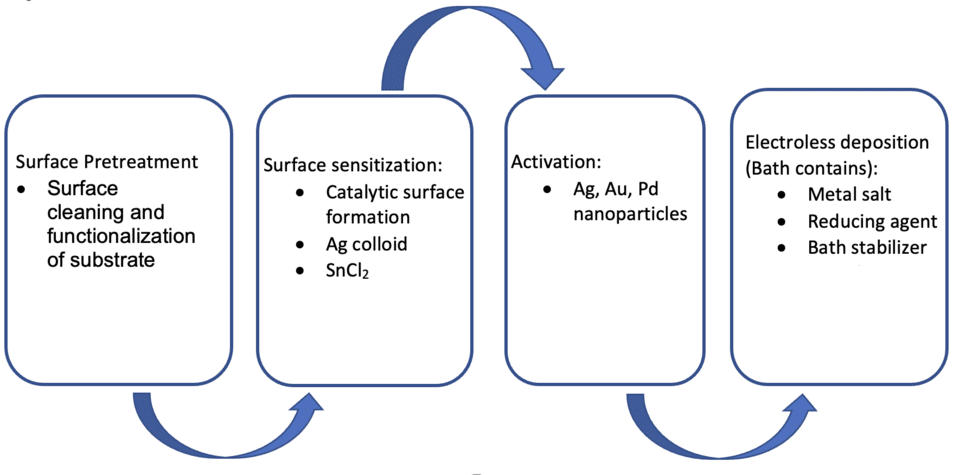
Étapes clés du processus de revêtement ED : Nous divisons le processus ED en quatre étapes principales :
- Prétraitement (nettoyage et préparation de surface) : Tout d'abord, le cadre est soigneusement nettoyé et prétraité pour éliminer toute saleté, huile ou oxyde. Cela comprend souvent un dégraissage et une couche de conversion (comme un rinçage au phosphate) pour garantir que le métal est prêt à adhérer à la peinture. Un prétraitement approprié est essentiel : une surface propre garantit une adhérence optimale du revêtement ED, sans contaminants.
- Immersion et électrodéposition : Ensuite, le cadre est immergé dans un bain de peinture électrolytique, à base d'eau et contenant des particules de peinture (généralement une résine époxy ou acrylique) dispersées dans une solution. Nous connectons le cadre à un circuit électrique comme une électrode (cathode ou anode selon le type de peinture, bien que la plupart des revêtements ED modernes soient cathodique (pour une meilleure résistance à la corrosion). Lorsqu'une tension est appliquée au bain, les particules de peinture chargées sont attirées vers le cadre de charge opposée et commencent à recouvrir chaque surface exposée . Parce que le cadre est entièrement immergé, même les coins et recoins complexes ou les zones internes proches des ouvertures sont couverts. (Par exemple, un cadre de vélo en acier placé dans un réservoir ED attirera les particules de peinture à la fois vers l'extérieur et vers toutes les surfaces intérieures accessibles par la solution, ce qui donnera une couche d'apprêt extrêmement uniforme.) L'épaisseur du revêtement peut être contrôlée avec précision en ajustant la tension électrique et le temps de bain, ce qui nous permet d'obtenir un film mince et uniforme, généralement de l'ordre de 15 à 30 microns d'épaisseur.
- Rinçage: Une fois l'épaisseur souhaitée atteinte, le cadre est retiré du bain. Nous le rinçons ensuite avec une solution spéciale ou de l'eau déionisée pour éliminer l'excédent de peinture solide qui ne s'est pas complètement déposé (souvent appelé « couche de crème »). Cette étape garantit une finition lisse, sans coulures ni flaques. La peinture éliminée à cette étape est généralement filtrée et recyclée dans le bain. les déchets sont minimisésEn fait, le revêtement ED est très efficace en termes d’utilisation de la peinture : la majeure partie de la peinture se retrouve sur le produit plutôt que d’être perdue par pulvérisation excessive, contrairement à la peinture conventionnelle.
- Cuisson (durcissement) : Après rinçage, le cadre est placé dans un four de cuisson. Il est cuit à une température appropriée (souvent autour de 150-200 °C) pendant une durée déterminée. guérir Le revêtement. Le durcissement réticule chimiquement la peinture, la transformant en un film dur et durable, collé au métal. Il en résulte une peinture très résistante. couche d'apprêt qui résiste à la corrosion et aux rayures. À ce stade, le cadre est généralement recouvert d'une fine couche de finition noire ou grise. De nombreux fabricants de vélos appliquent ensuite une couche de finition (par exemple, un revêtement en poudre ou une peinture liquide) par-dessus cet apprêt pour la couleur et une protection supplémentaire. Cependant, même seule, la couche de finition offre déjà une protection robuste.
La beauté de ce processus ED réside dans la façon dont complet et cohérent La couverture est optimale. Le champ électrique déposant naturellement la peinture uniformément jusqu'à ce que le revêtement atteigne une épaisseur définie (à ce stade, la pièce est isolée et le dépôt ralentit), le cadre présente une couche très uniforme, même sur des formes complexes. En tant qu'ingénieurs chez Regen Tech, nous savons que le revêtement par électrophorèse (ED) peut atteindre des zones que les pistolets de pulvérisation pourraient manquer et qu'il crée un film adhérent au niveau moléculaire pour une protection maximale.
Science des matériaux : pourquoi les revêtements électrolytiques préviennent la corrosion
Du point de vue de la science des matériaux, les revêtements ED excellent en raison de la combinaison de physique et chimie En jeu. La peinture ED elle-même est généralement formulée à partir d'une résine époxy ou acrylique avec des pigments anticorrosion. Les peintures ED à base d'époxy sont couramment utilisées comme apprêts dans l'industrie automobile en raison de leur excellente adhérence et de leur résistance chimique (bien qu'elles nécessitent généralement une couche de finition, car les époxydes peuvent fariner sous l'effet des UV). Le procédé ED dépose un film dense et sans piqûres. Ceci est important pour la corrosion, car toute fissure dans un revêtement peut devenir un point de départ pour la rouille sur l'acier. Avec l'ED, la couverture est si uniforme que même les bords, les soudures et les cavités cachées sont protégés. sans les taches fines qui affligent souvent les travaux de peinture réalisés à la main.
Lorsque les particules de peinture chargées frappent le cadre métallique pendant le dépôt, elles neutraliser la charge et coalescer en un film continu. L'étape de cuisson réticule ensuite fermement ce film. Le résultat est comparable à l'enveloppement du métal dans une coque plastique imperméable. L'humidité, l'oxygène et les sels, ennemis du métal nu, ne pénètrent pas facilement un revêtement électrolytique intact. Lors de tests en laboratoire, les panneaux d'acier électrolytiques résistent à des centaines, voire des milliers d'heures dans des chambres de brouillard salin avant de présenter de la rouille rouge. Par exemple, les revêtements époxy peuvent atteindre Plus de 1 000 heures en brouillard salin Tests sans corrosion, notamment avec un prétraitement approprié comme le phosphate de zinc. Ce niveau de performance dépasse largement celui d'une peinture liquide monocouche classique. C'est l'une des raisons pour lesquelles les constructeurs automobiles utilisent des apprêts ED depuis des décennies Sur les carrosseries, on s'attend à ce qu'une voiture survive à plus de dix hivers sur des routes salées. Nous souhaitons la même longévité pour le cadre de votre vélo électrique ou cargo.
Un autre avantage technique est que les revêtements ED conservent une forte adhésion Au fil du temps, le dépôt électrique permet au revêtement d'entrer en contact étroit avec le métal à l'échelle microscopique, favorisant ainsi l'adhérence par attraction électrostatique et liaison chimique. Même si le cadre du vélo fléchit sous l'effet d'une charge ou d'un impact, la couche électrodéposition est moins susceptible de s'écailler ou de se décoller qu'une peinture épaisse et cassante, car elle est relativement fine et adhère presque comme une seconde peau. En fait, la couche électrodéposition constitue souvent un excellent apprêt sous d'autres revêtements, améliorant également leur adhérence. Chez Regen Tech, nous appliquons souvent une peinture en poudre ou une couche de finition polyuréthane sur nos cadres traités par électrodéposition ; la couche électrodéposition assure une adhérence parfaite à la couche de finition et empêche toute corrosion sous-couche, même en cas de rayure.
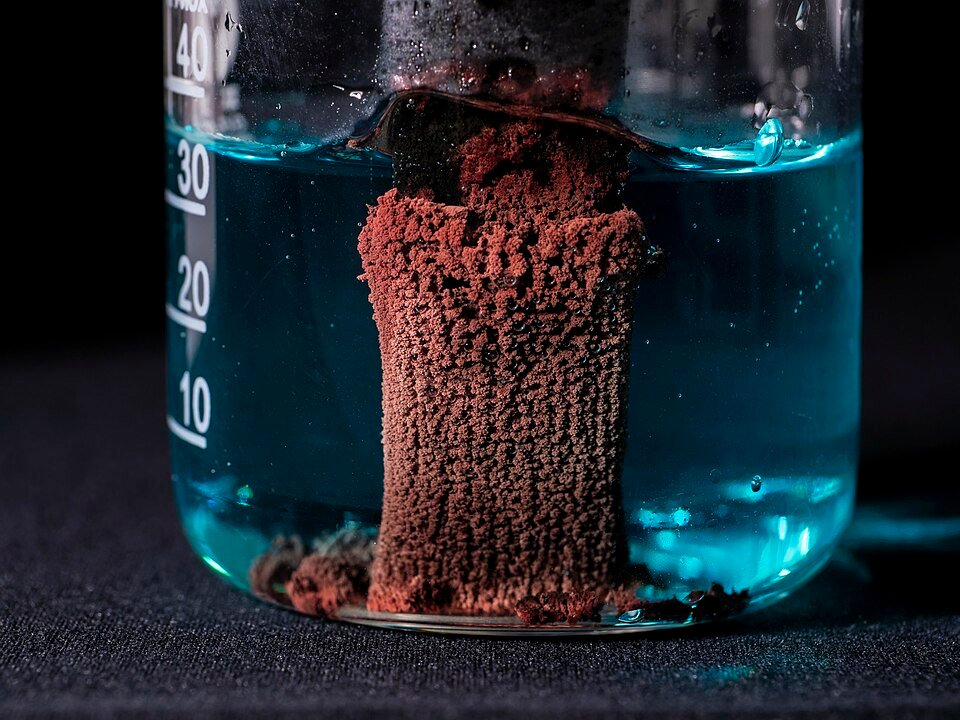
En résumé, le secret de la science des matériaux est : une couche fine, uniforme et plastifiée avec une couverture parfaite = une barrière robuste contre la rouille. C'est pourquoi un cadre en acier traité avec un revêtement ED peut survivre à des années de conditions humides et salées avec un minimum de rouille, tandis qu'un cadre non traité ou mal peint peut présenter de la rouille rampante après un seul hiver si la peinture s'écaille.
Principaux avantages du revêtement ED pour les cadres de vélo
Pourquoi se donner la peine de revêtir un cadre de vélo avec un revêtement ED ? Voici ses principaux avantages et comment ils se traduisent concrètement :
- Résistance supérieure à la corrosion : Le principal avantage est la protection contre la rouille. Un cadre avec revêtement ED est très résistant à la corrosion, car le revêtement scelle complètement le métal. Même l'intérieur des tubes et les joints serrés sont protégés. Ceci est crucial pour les cadres de vélos électriques et cargos en acier exposés à la pluie. Par exemple, Ritchey cite spécifiquement le revêtement ED sur ses cadres en acier. « pour la résistance à la corrosion » En substance, le revêtement ED prolonge considérablement la durée de vie des cadres en acier en les protégeant de la redoutable rouille brune. Les cadres en aluminium (qui ne rouillent pas comme l'acier) en bénéficient également : le revêtement ED prévient l'oxydation et les piqûres de surface, et favorise l'adhérence de la peinture à la couche d'oxyde de l'aluminium.
- Couverture uniforme et fine : Les revêtements ED sont minces et uniformes, généralement de 15 à 25 microns d'épaisseur (environ un demi-millième de pouce). Cette uniformité signifie pas de coulures, de gouttes ou d'accumulation importante dans les coins. Il est également très léger et ne masque pas les détails délicats comme les numéros de série ou les pattes complexes. Contrairement au revêtement en poudre, plus épais, l'ED peut recouvrir formes complexes et cavités internes Uniformément. Idéal pour les cadres de vélos cargo complexes comportant de nombreuses soudures, goussets et brasures pour porte-bagages. Chaque élément du cadre bénéficie d'une protection égale.
- Forte adhérence et durabilité : Les revêtements ED forment une couche intégrale sur le métal, offrant une excellente résistance à l'écaillage. Si une petite pierre heurte le dessous d'un cadre de vélo, un apprêt ED risque moins de s'écailler qu'une peinture traditionnelle grâce à sa forte adhérence. flexible Suffisamment pour absorber les chocs mineurs. De plus, souvent utilisé comme apprêt sous une couche de finition, le système bicouche (apprêt ED + poudre ou peinture de finition) améliore considérablement la durabilité globale. La couche ED empêche l'humidité de s'infiltrer sous la couche de finition, même en cas d'éraflure. Cette approche « ceinture et bretelles » (apprêt + peinture) explique pourquoi les fabricants de vélos haut de gamme utilisant l'ED ont moins de problèmes de cloquage de peinture ou de rouille naissante à partir d'une rayure. La couche ED isole les dommages à cet endroit précis, empêchant la rouille de se propager sous la peinture.
- Économies à long terme : Bien que le revêtement par électroérosion nécessite des équipements sophistiqués (cuves, systèmes électriques, fours), il peut être économique à long terme pour les fabricants et les propriétaires de motos. Les fabricants en bénéficient. débit élevé et retouches minimales— le processus est hautement automatisé et cohérent, ce qui réduit le travail de retouches ou de repeinture. De plus, le gaspillage de peinture est minime, ce qui diminue les coûts de matériaux. Pour les propriétaires de vélos ou les gestionnaires de flotte, un cadre qui n'a pas besoin d'être remplacé ou traité constamment contre la rouille représente une économie considérable à long terme. Un vélo cargo bien protégé peut rester en service pendant de nombreuses années (ou des dizaines de milliers de kilomètres) sans problème de corrosion structurelle, ce qui représente un meilleur retour sur investissement.
- Respect de l'environnement : Le revêtement ED est relativement écologique par rapport à de nombreuses méthodes de peinture traditionnelles. Ce procédé est à base d'eau et contient peu ou pas de composés organiques volatils (COV) Cela signifie moins de fumées nocives et un impact environnemental moindre. Les excédents de peinture sont récupérés, minimisant ainsi les déchets. Pour les entreprises (et les clients) de l'UE, où les normes environnementales sont strictes, c'est un atout majeur. Cela s'inscrit dans la philosophie de développement durable du cyclisme lui-même. Chez Regen Tech, nous sommes conscients que les opérations de revêtement par électroérosion peuvent respecter des réglementations environnementales strictes tout en offrant un produit de qualité supérieure.
- Cohérence et contrôle de la qualité : L'ED est un processus très contrôlé : chaque image passe par les mêmes étapes, avec une tension, un temps d'immersion et un programme de cuisson surveillés. Cela garantit une qualité constante. Si vous êtes ingénieur ou responsable de marque, cette reproductibilité est essentielle. moins de réclamations sous garantie et une finition protectrice fiable sur laquelle vous pouvez compter pour chaque lot de production. Elle n'est pas soumise aux variations de la peinture manuelle ni aux conditions ambiantes. Nous aimons dire que le réservoir ED n'a pas de « mauvais jours » ; il est traité de la même manière à chaque fois, garantissant ainsi à chaque cadre de vélo un traitement royal.
En bref, le revêtement ED combine le meilleur des deux mondes : il est hautement protecteur comme une peinture épaisse, mais léger et précis comme une fine pellicule. Ces avantages se traduisent directement par des vélos durent plus longtemps, sont plus beaux et conservent leur intégrité même lorsqu'il est utilisé durement.
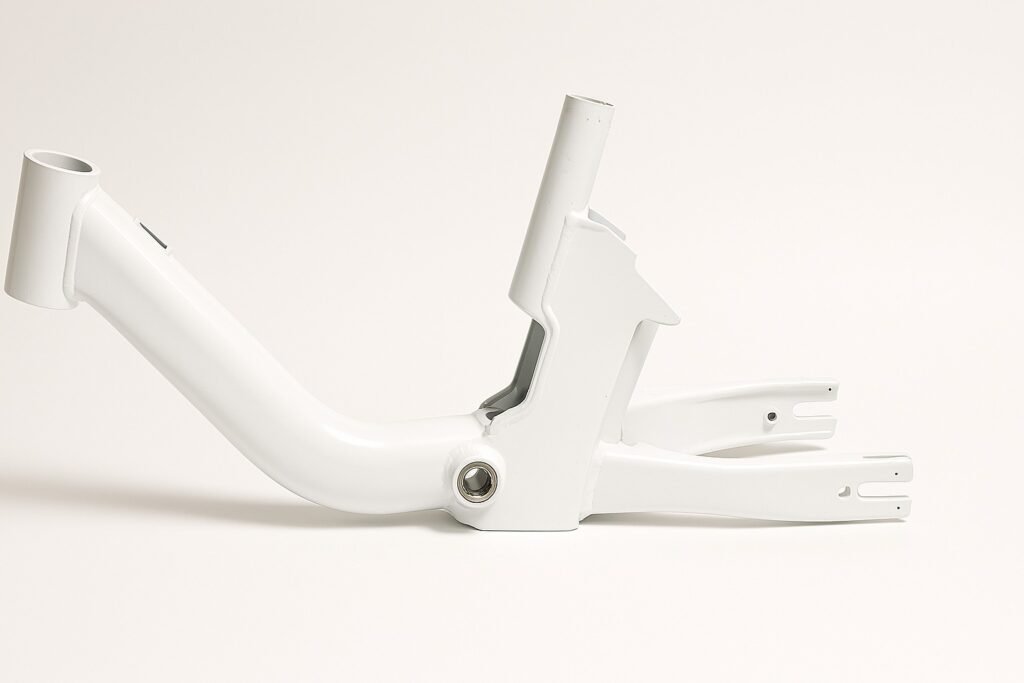
Revêtement par poudre, revêtement par extrusion et peinture humide : comparaison
Vous vous demandez peut-être comment le revêtement ED se compare aux méthodes de finition de vélo plus courantes, comme le thermolaquage ou la peinture au pistolet traditionnelle. Chaque méthode a ses avantages ; comparons donc leurs avantages et leurs inconvénients pour les cadres de vélo :
- Revêtement en poudre : Il s'agit d'une finition courante pour de nombreux vélos. Le revêtement par poudre consiste à appliquer électrostatiquement une poudre sèche sur le métal, puis à la cuire pour former une coque dure. Ses points forts : une résistance et une épaisseur exceptionnellesLa poudre forme une couche plus épaisse que l'ED, ce qui est idéal pour la résistance aux chocs et aux rayures. Elle est souvent résistante aux UV et existe en de nombreuses couleurs et textures (brillante, mate, métallisée, etc.). Une fois durcie, une peinture en poudre peut supporter de nombreux abus sans s'écailler. Cependant, elle peut parfois être trop épais Il a tendance à s'infiltrer dans les espaces très étroits ou à l'intérieur de tubes de petit diamètre. Il a tendance à recouvrir fortement les surfaces extérieures, mais peut laisser les surfaces intérieures ou les creux profonds moins couverts (en raison de l'effet « cage de Faraday » dans les angles étroits). De plus, un revêtement en poudre monocouche n'empêche pas toujours la corrosion en cas d'écaillage : la rouille peut se former à partir d'une fissure du revêtement et s'infiltrer en dessous. C'est pourquoi certains fabricants haut de gamme utilisent un système double : couche ED comme apprêt, puis couche de poudre par-dessus pour la couleur et la protection UV. La couche ED garantit l'absence de corrosion, et la poudre ajoute résistance aux chocs et esthétique. qualité de finitionLa poudre a un aspect lisse, mais n'offre pas la précision ultra-fine de l'ED ; les détails les plus fins peuvent être légèrement arrondis par le revêtement. En termes de poids, la poudre est plus lourde par unité de surface (en raison de son épaisseur), mais sur un cadre de vélo, la différence n'est que de quelques dizaines de grammes par rapport à l'ED. Le revêtement en poudre est également un respectueux de l'environnement procédé (pas de COV, les projections peuvent être récupérées), mais la nécessité d'un four à haute température et d'un masquage minutieux des filetages ou des surfaces d'appui est une considération dans la fabrication.
- Peinture humide (peinture liquide) : La peinture humide traditionnelle (utilisant des peintures à base de solvant ou d'eau pulvérisées et séchées à l'air ou au four) offre options de couleurs et de styles illimitéesLes fabricants de motos custom utilisent souvent la peinture liquide pour les graphismes complexes, les dégradés ou les travaux ponctuels. L'équipement requis est plus simple (un pistolet et une cabine ventilée). Cependant, la peinture liquide est généralement moins durable Que l'ED ou la poudre. Plus fine, elle est plus sujette aux écaillages et aux rayures. Les peintures humides de haute qualité sur les vélos nécessitent généralement plusieurs couches : un apprêt, des couches de couleur et un vernis transparent pour une durabilité optimale. Même avec cette couche, une finition peinte humide ne résiste généralement pas aussi bien aux projections de pierres ou aux chutes qu'une peinture en poudre. Du point de vue de la corrosion, si la couche de peinture est percée, la rouille peut apparaître assez rapidement sur un cadre en acier. De plus, la peinture humide contient souvent des solvants, ce qui signifie émissions de COV plus élevées Lors de l'application. L'avantage est que la peinture liquide est plus facile à retoucher et ne nécessite pas de fours à 180 °C (risquant de se déformer si le métal est fin ou si des pièces thermosensibles sont fixées). Cependant, pour les grands vélos cargo, la pulvérisation uniforme de peinture liquide peut s'avérer délicate en raison de leur taille et de leur forme, et le revêtement de toutes les fissures dépend des compétences du peintre. En général, la peinture liquide est utilisée pour les productions à petite échelle ou sur mesure, tandis que l'ED et la poudre sont privilégiées pour les productions à plus grande échelle pour leur efficacité et leur robustesse.
Combinaison de méthodes : Ce n'est pas toujours l'un ou l'autre. Dans de nombreux cas, le revêtement ED est utilisé. en combinaison Avec de la peinture en poudre ou liquide. Considérez l'électrodéposition comme la couche de base ultime (apprêt). Par exemple, certains fabricants de vélos cargo appliquent une électrodéposition sur le cadre brut pour une protection complète contre la corrosion, à l'intérieur comme à l'extérieur, puis une peinture en poudre pour une coque extérieure robuste et la couleur souhaitée. Le résultat est un cadre à double protection : si la couche supérieure en poudre s'écaille, la couche d'électrodéposition en dessous empêche la rouille. Chez Regen Tech, nous utilisons cette méthode pour les cadres haut de gamme, car elle offre une finition à la fois résistante et esthétique. Schuette Metals, un finisseur, souligne que l'utilisation combinée d'une électrodéposition et d'une couche de finition permet d'obtenir « protection maximale » combinant la résistance à la corrosion du revêtement électronique avec l'endurance d'un revêtement en poudre.
Pour résumer la comparaison, voici un bref aperçu de avantages et inconvénients:
- Revêtement ED (dépôt électrophorétique) : Avantages : Meilleure couverture (même dans les zones complexes et les intérieurs de tubes), excellente résistance à la corrosion en tant qu'apprêt mince, film mince très uniforme, excellente adhérence, processus respectueux de l'environnement. Inconvénients : Nécessite généralement une couche de finition pour la protection UV ou la couleur, nécessite un équipement et un réservoir spécialisés (pas facile pour les amateurs), l'intérieur des tubes scellés très longs peut toujours ne pas obtenir de couverture 100% (ED pénètre dans les cavités sur une certaine distance, mais pas indéfiniment en profondeur sans une ouverture aux deux extrémités).
- Revêtement en poudre : Avantages : Très résistant aux chocs/écaillages, une couche épaisse peut couvrir de légères imperfections de surface, de nombreuses options de couleur/texture, aucune émission de COV, efficace pour le traitement par lots. Inconvénients : Ne peut pas facilement recouvrir les surfaces internes ou les endroits extrêmement étroits (application en ligne de mire), couche plus épaisse et plus lourde, la chaleur de durcissement peut être un problème pour les composants assemblés, plus difficile à retoucher ou à repeindre (l'ancienne poudre doit être enlevée), et si utilisé seul, un éclat peut laisser la rouille commencer en dessous.
- Peinture humide : Avantages : Couleur illimitée et liberté artistique, faible coût initial de l'équipement, peut être appliqué en couches plus fines pour économiser du poids (si la durabilité est moins une préoccupation), facile à retoucher sur de petites zones, idéal pour les travaux personnalisés. Inconvénients : Durabilité la plus faible – sujet aux rayures, aux éclats et à la décoloration, sauf si un système multicouche est utilisé ; COV plus élevés et déchets de pulvérisation (sauf si des peintures modernes à base d'eau sont utilisées) ; la couverture sur des formes complexes dépend de la minutie du peintre ; des temps de séchage plus longs (séchage à l'air) peuvent ralentir la production.
Pour les équipes d'ingénieurs et les concepteurs de vélos, le choix se résume souvent au cas d'utilisation : un vélo cargo utilitaire robuste qui vit à l'extérieur 24 heures sur 24, 7 jours sur 7, peut justifier le approche ceinture et bretelles de la dysfonction érectile + poudreUn vélo de boutique pourrait privilégier une peinture personnalisée pour son esthétique, acceptant ainsi un entretien plus approfondi. Chez Regen Tech, nous privilégions la longévité et les performances du cadre. C'est pourquoi nous préconisons le revêtement ED pour tout vélo exposé aux conditions climatiques et aux abus du monde réel.
Intéressé par un vélo cargo personnalisé ?
Nous aimerions en savoir plus sur les besoins de votre entreprise, que vous envisagiez une collaboration OEM ou ODM, des opportunités de vente en gros ou un partenariat à long terme. N'hésitez pas à nous fournir des estimations de quantités ou d'autres informations clés.
Vélos cargo dans l'UE : l'importance du revêtement ED
Les vélos cargos des villes européennes sont très performants : imaginez un vélo cargo électrique de livraison pédalant sous la pluie à Amsterdam ou un vélo cargo familial garé dehors en plein hiver allemand. La volonté de l'UE de promouvoir une logistique plus verte implique que davantage de vélos cargos remplacent les camionnettes, mais aussi que ces vélos remplaceront les camionnettes. ne peut pas se cacher du mauvais tempsLes cadres sont régulièrement mouillés et, en hiver, le sel de voirie peut être très corrosif pour le métal. Par exemple, les pays d'Europe du Nord salent souvent les routes pour lutter contre le verglas, et l'air salin des zones côtières peut attaquer agressivement un cadre en acier non protégé. Avec le temps, même un petit éclat de peinture peut se transformer en une vilaine plaque de rouille.
Des cas concrets illustrent cette vulnérabilité. Babboe, célèbre marque néerlandaise de vélos cargo, a d'ailleurs été confrontée à une crise en 2023. plus de 9 000 vélos cargo ont été rappelés en raison de fissures et de bris de cadres. Les enquêtes ont révélé que corrosion des matériaux La rouille a été l'une des principales causes de fragilisation de ces cadres. Les zones de forte contrainte ont connu une propagation qui, combinée à des défauts de fabrication, a entraîné des défaillances. Ceci met en évidence un point crucial : la corrosion n'est pas seulement esthétiqueCela peut poser un problème de sécurité structurelle. Un cadre de vélo cargo transporte une charge précieuse (souvent des enfants ou des livraisons) ; une défaillance est dangereuse et porte atteinte à la réputation. Des mesures anticorrosion robustes, comme le revêtement ED, auraient pu atténuer considérablement la rouille dans ces zones à forte contrainte, prévenant ainsi des problèmes aussi répandus.
Pour un vélo cargo européen, le revêtement ED est une évidence : il protège efficacement le cadre des intempéries. Imaginez un cadre avec revêtement ED comme une armure toutes saisons. Laissez-le dehors sous la pluie, l'eau ne s'infiltre pas sous la peinture. Roulez dans la neige fondue hivernale, et le sel ne fait que mouiller la coque peinte, sans ronger l'acier en dessous. Même à l'intérieur du cadre, le revêtement ED recouvre les surfaces intérieures accessibles aux extrémités des tubes ou aux orifices d'aération, offrant une protection interne là où la peinture normale n'atteint jamais. (De nombreux vélos cargo sont dotés de petits orifices ou ouvertures de drainage aux joints des tubes, spécialement conçus pour permettre à la solution de revêtement ED de s'écouler et de recouvrir ces surfaces internes pendant la fabrication.)
Les vélos cargo ont également tendance à avoir des supports et des articulations soudés plus nombreux, ainsi que des formes de cadre complexes (pour les vélos à godets ou à longs pédaliers). Ce sont des domaines où la peinture au pistolet traditionnelle peut manquer des endroits, ou là où la rouille a tendance à se former (comme autour des soudures). L'ED excelle ici en immergeant complètement le cadre : chaque soudure est soigneusement recouverte et l'épaisseur de la peinture est uniforme, même dans les angles. Cette uniformité évite tout point faible propice à la rouille. Nous expliquons souvent aux revendeurs de vélos cargo qu'un cadre traité par ED est beaucoup plus facile à entretenir: vous ne trouverez pas de bulles de rouille sous la peinture un an plus tard, nécessitant un ponçage et des retouches. Le cadre peut survivre près de la côte ou aux hivers berlinois avec un minimum de risques de corrosion.
Il est important de noter que les consommateurs et les entreprises européens exigent de la longévité. Un vélo cargo est un investissement, souvent aussi cher qu'une voiture d'occasion. Ils souhaitent qu'il dure de nombreuses années. Le revêtement ED permet aux fabricants d'offrir en toute confiance des garanties contre la corrosion du cadre. Par exemple, une marque pourrait offrir une garantie antirouille de 5 à 10 ans sur un cadre traité ED, ce qui serait risqué sur un cadre en acier non protégé. Pour une utilisation en flotte (comme les vélos de livraison postale ou les vélos cargo municipaux), les cadres traités ED offrent une coût total de possession inférieur: les vélos n'auront pas besoin d'être mis au rebut prématurément à cause de la rouille, et ils conserveront leur aspect professionnel avec moins d'efforts. Même pour les vélos cargo en aluminium, qui ne rouillent pas de la même manière, l'ED prévient l'oxydation crayeuse et la corrosion sous-peinte qui peuvent encore se produire, et favorise l'adhérence de la peinture afin d'éviter l'écaillage généralisé des éclats.
En bref, le climat et les conditions d'utilisation de l'UE poussent la durabilité des vélos à ses limites. Le revêtement ED est notre solution pour garantir que ces vélos performants relèvent ce défi. Tranquillité d'esprit garantie : qu'il pleuve, qu'il neige ou qu'il vente, un cadre de vélo cargo avec revêtement ED est idéal. construit pour durerEn tant que Regen Tech, lorsque nous collaborons avec des marques de vélos cargo de l'UE, nous soulignons que le revêtement ED n'est pas seulement une étape supplémentaire - c'est une proposition de valeur à long terme pour le fabricant et le cycliste, gardant le vélo sûr, sain et en service aussi longtemps que possible.
Avantages concrets pour les détaillants et les marques
Du point de vue de l'entreprise et de l'utilisateur, le revêtement ED offre des avantages tangibles :
- Pour les détaillants de vélos et les propriétaires de magasins : Vendre des vélos avec un cadre traité par électrophorèse (ED) réduit les réclamations clients. Imaginez vendre un vélo cargo électrique à une famille ou à une entreprise de logistique en sachant que le cadre ne reviendra pas dans un an avec des problèmes de rouille. Cela renforce la confiance et la réputation de qualité. Cela réduit également les réclamations sous garantie et les réparations liées à la corrosion. Un autre avantage est que les vélos conservent leur esthétique plus longtemps en salle d'exposition : un cadre traité par électrophorèse (ED) avec une bonne couche de finition ne présente pas de petites taches de rouille au niveau des soudures ni d'éclats, de sorte que même les modèles de démonstration et les modèles de démonstration restent impeccables. Les commerçants peuvent mettre en avant le « revêtement anticorrosion de qualité automobile » comme argument de vente, en expliquant aux clients que le cadre de leur vélo bénéficie de la même protection qu'un châssis de voiture. C'est particulièrement convaincant pour les vélos électriques et cargos haut de gamme, pour lesquels les clients réalisent un investissement important. Ils veulent avoir l'assurance que le cadre (le cœur du vélo) est bien protégé.
- Pour les exploitants de flottes et les services de location : Si vous exploitez une flotte de vélos cargo (par exemple, un système de partage de vélos en ville ou un service de livraison), les cadres à revêtement ED équivalent à moins de frais de maintenanceLes vélos peuvent être lavés régulièrement sans craindre que l'eau ne s'infiltre et ne rouille dans les zones cachées. Il est moins nécessaire de démonter régulièrement les vélos pour appliquer des inhibiteurs de rouille à l'intérieur (une pratique parfois utilisée sur les cadres en acier non traités). Globalement, les temps d'immobilisation du parc sont réduits. Certains gestionnaires de parc que nous avons interrogés apprécient la possibilité d'utiliser des vélos avec un revêtement ED. revendu avec une valeur plus élevée Après quelques années d'utilisation, les cadres ne paraissent pas abîmés par la rouille. La longévité offerte par ED permet même aux utilisateurs d'occasion d'en bénéficier.
- Pour les responsables de marques de vélos et les concepteurs de produits : L'intégration du revêtement ED à votre processus de fabrication peut améliorer la perception de qualité de votre marque. Cela vous permet de commercialiser vos vélos comme produits haut de gamme et hautement durables adaptés à une utilisation réelleEn Europe et ailleurs, les clients avertis s'interrogent sur la protection anticorrosion des cadres, surtout s'ils ont déjà été brûlés par un vélo rouillé. Pouvoir affirmer que « nos cadres sont traités par électrophorèse (ED) comme les cadres automobiles, vous offrant ainsi une tranquillité d'esprit face à la rouille » est un argument de poids. De plus, le revêtement ED s'inscrit dans les objectifs de développement durable : un vélo qui dure plus longtemps est plus durable qu'un vélo qui doit être mis au rebut et remplacé plus tôt. Et comme le revêtement ED est respectueux de l'environnement lors de sa production (faible teneur en COV, utilisation efficace de la peinture), il peut s'inscrire dans le discours écologique d'une marque. Côté production, si la mise en place du revêtement ED représente un coût initial, la réduction des retouches de peinture, l'homogénéité et la possibilité de rationaliser l'apprêt et la peinture sur une seule ligne automatisée peuvent améliorer la productivité de l'usine. Des marques comme Surly (connue pour ses vélos d'aventure en acier) ont adopté le revêtement ED sur tous leurs cadres pour garantir leur longévité, un atout majeur pour les cyclistes qui utilisent ces vélos dans des environnements difficiles.
- Service après-vente simplifié : Autre avantage : si un cadre est endommagé ou nécessite une modification, les cadres traités par électrodéposition sont plus faciles à retoucher. La couche électrodéposition étant une base parfaite, toute nouvelle peinture ou réparation adhèrera parfaitement. Nous avons constaté que même si vous devez souder un petit support ultérieurement (ce qui brûle le revêtement à cet endroit), le revêtement électrodéposition environnant n'a pas tendance à se décoller ni à se décoller. Vous pouvez réparer la zone et repeindre, et le reste du cadre reste protégé. Cette résilience simplifie la tâche des techniciens de maintenance et prolonge la durée de vie des vélos.
- Tranquillité d'esprit du client : Au final, le conducteur ou l'utilisateur du vélo bénéficie du revêtement ED d'une manière dont il ne se rend peut-être même pas compte : il ne rencontre aucun problème. Son cadre ne rouille pas discrètement de l'intérieur, sa peinture ne fait pas de bulles aux joints après un hiver et il ne voit pas de traces de rouille orange après la pluie. Au contraire, son vélo reste solide et esthétique. Cela améliore la satisfaction et la fidélité des clients. Un propriétaire de vélo cargo avec revêtement ED est plus susceptible de conserver cette marque lors de son prochain achat, ayant constaté la différence de durabilité.
D'après notre expérience, il est essentiel de sensibiliser les détaillants et les utilisateurs finaux au revêtement ED. Une fois que les clients comprennent que leur cadre de vélo a subi ce processus avancé, ils apprécient souvent le résultat. valeur cachée C'est comme une police d'assurance intégrée au vélo. Pour les entreprises, cela permet de différencier leur produit sur un marché concurrentiel où tous les cadres ne se valent pas. Et pour un commerçant qui traite avec une clientèle avertie, c'est un atout supplémentaire pour conclure une vente.
Conclusion : Revêtement ED – Un investissement judicieux en matière de durabilité
À Regen TechNous sommes les fervents défenseurs du revêtement ED, car nous avons pu constater par nous-mêmes comment il prolonge la durée de vie des vélos électriques et des vélos cargo. Le procédé peut paraître complexe (immerger les cadres dans des bains de peinture électrifiés et les cuire), mais le résultat est simple : un cadre résistant. Le revêtement ED répond aux besoins fondamentaux des vélos modernes soumis à une utilisation intensive : résistance à la corrosion, durabilité et fiabilitéIl s'agit d'une technologie qui encapsule un cadre dans un bouclier protecteur, un peu comme celui utilisé sur les automobiles, mais adapté aux vélos.
Nous avons examiné le procédé ED et ses avantages, l'avons comparé à d'autres méthodes de revêtement et avons examiné son intérêt particulier pour les vélos cargos utilisés dans les jungles urbaines européennes. Il est clair qu'un cadre de vélo avec revêtement ED et une couche de finition de qualité est bien mieux équipé pour supporter des années de service qu'un cadre sans. C'est une façon de pérenniser votre produit. Pour les cyclistes et les passionnés, cela signifie plus de sorties et moins de soucis. Pour les ingénieurs et les responsables de marque, cela signifie que votre conception et votre réputation résistent à l'épreuve du temps (et des intempéries). Et pour les détaillants, cela signifie vendre un produit dont vous savez qu'il saura satisfaire vos clients sur le long terme.
Dans un monde où nous demandons de plus en plus à nos vélos électriques et vélos cargos (transporter des charges plus lourdes, remplacer les voitures, fonctionner toute l'année), investir dans une protection de cadre avancée n'est pas un luxe, mais une nécessité intelligente. Le revêtement ED est un choix intelligentIl allie science des matériaux de pointe et performance pratique. En enseignant et en utilisant cette technologie, nous, chez Regen Tech, souhaitons garantir que les vélos qui propulsent le mouvement de mobilité verte soient à la hauteur de la tâche, non seulement aujourd'hui, mais pour de nombreuses années.
En conclusion, le revêtement ED n'est peut-être pas visible une fois le vélo peint et assemblé, mais ses effets le seront certainement : vous le verrez sur une flotte de vélos de livraison qui ne rouillent pas, ou sur un vélo cargo apprécié qui conserve son éclat après d'innombrables trajets sous la pluie. C'est l'importance du revêtement ED pour les vélos électriques et les vélos cargo : une conduite plus robuste et plus durable, et une nouvelle façon d'innover pour assurer la fiabilité des cyclistes et de leur équipement.
Roulez sans rouille ! Avec les cadres à revêtement ED, c'est une chose de moins à laquelle penser et une raison de plus de faire confiance à votre vélo à chaque trajet.
Sources : Les informations et données présentées ici sont étayées par des recherches et des exemples du secteur, notamment des informations sur la fabrication et des études comparatives sur les performances des revêtements, comme cité tout au long de l'article.