Teherkerékpár OEM/ODM megoldásszolgáltatóként, mi az Regen-nél Tudd, hogy egy kerékpár váza a gerince. A váz szilárdsága nem csak a kerékpár megtartását jelenti; hanem a drága rakomány biztonságos szállítását, a mindennapi használat évekig tartó kitartását és a kerékpárosok önbizalmának megteremtését is. Ebben a cikkben első kézből vizsgáljuk meg, hogy mi határozza meg igazán egy teherkerékpár vázának tartósságát. Elmélyülünk az anyagtudományban, a geometriában, a hegesztési varratok integritásában, a vizsgálati módszerekben, a korrózióvédelemben, a gyártási pontosságban és a valós terhelésdinamikában – mindezt a teherkerékpárok lencséjén keresztül. Útközben megosztunk néhány saját tapasztalatunkból származó meglátást (beleértve a portugáliai összeszerelésünket és a kínai vázgyártásunkat), és további forrásokhoz irányítjuk a figyelmet a mélyebb elmélyüléshez. Akár a kerékpáripar szakembere, akár rajongó vagy, reméljük, hogy ez egy világos, meleg és átfogó útmutatót nyújt arról, hogy mi teszi tartóssá egy teherkerékpár vázát.
(Új a teherbiciklik világában? Nézd meg átfogó Teherautó-kerékpár 101 útmutató a kulcsfontosságú fogalmak és fogalmak bemutatásához.)
Anyagtudomány: A váz szilárdságának alapjai
Az anyagválasztás az egyik legfontosabb tényező a váz tartóssága szempontjából. A különböző vázanyagok – az alumíniumtól és acéltól a szénszálon át – mindegyike egyedi tulajdonságokkal rendelkezik, amelyek befolyásolják a szilárdságot, a kifáradási élettartamot és a hosszú élettartamot. A teherkerékpárok esetében, amelyek nehezebb terheket szállítanak, mint a hagyományos kerékpárok, a megfelelő anyag kiválasztása kritikus fontosságú.
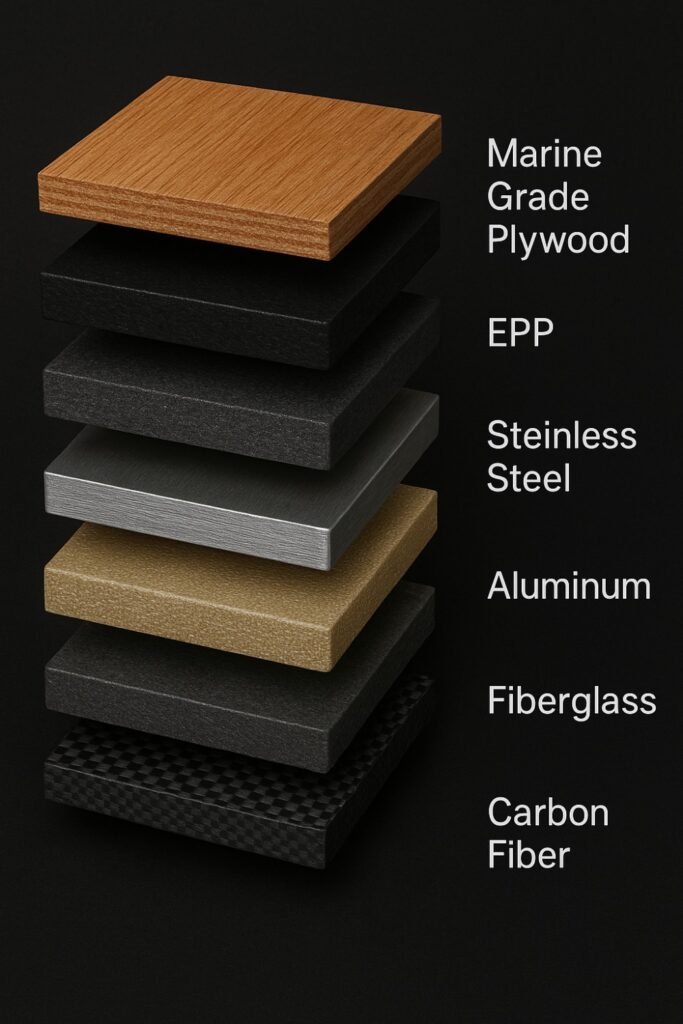
- Alumíniumötvözetek: Az alumínium rendkívül népszerű a modern teherkerékpárokban (beleértve a saját vázainkat is) könnyű súlya és jó merevség-tömeg aránya miatt. A kiváló minőségű alumíniumötvözetek, mint például a 6061-T6, erős, merev szerkezetet biztosítanak acél tömege nélkül. Az alumíniumnak azonban van egy fő hátránya: kevésbé tűri az ismétlődő igénybevételi ciklusokat, és gyorsabb fáradtság mint az acél. A gyakorlatban egy alumíniumváz élettartama rövidebb lehet intenzív használat esetén, és hamarabb kialakulhatnak rajta mikrorepedések vagy meghibásodások, ha nincs megfelelően megtervezve. Ez nem jelenti azt, hogy az alumíniumvázak gyengék – távolról sem. Megfelelő tervezéssel és hőkezeléssel (a T6 eljárás a hegesztés után újra igazítja a fém erezetszerkezetét) az alumíniumvázak biztonságosan elbírnak több száz kilogrammot (a saját...). RS01 teherbicikli A váz 6061-T6 ötvözetből készült, amely akár 250 kg hasznos terhet is elbír. Ez azt jelenti, hogy a mérnököknek figyelembe kell venniük a kifáradást vastagabb falú csövek vagy további megerősítések használatával a nagy igénybevételnek kitett területeken. (Kíváncsi, hogyan viszonyul az alumínium más fémekhez? Tekintse meg a Vázanyagok összehasonlítása: alumínium vs. acél vs. mások alaposabb vizsgálathoz.)
- Acél (nagy szakítószilárdságú és króm-molibdén): Az acél a klasszikus kerékpárváz anyag, és továbbra is az. igásló a tartósságértEgy jól megépített acélváz évtizedekig is kitarthat. Az acél inherens szívóssága és rugalmassága kiváló ellenállást biztosít a fém kifáradásával szemben. Képes elnyelni az ütéseket és rezgéseket (például kátyúkat vagy járdaszegély-leeséseket) repedés nélkül, ezért sok nagy teherbírású teherkerékpár vagy hosszúfarú váz acélt használ. Ezenkívül, ha egy acélváz megreped, gyakran hegesztéssel javítható – ami a hosszú távú használhatóság szempontjából előnyös. A hátrányok: az acél nehezebb, így a kerékpárt nehezebb pedálozni vagy emelni, és korrózióra hajlamos (rozsda), ha nincs védve. A tehergépkocsiknál a súly kevésbé fontos, mint a versenykerékpároknál, így a tartósságért tett kompromisszum általában megéri. Sok bakfiet (dobozos kerékpár) és kerékpár teherautó króm-molibdén acélötvözeteket használ, hogy kihasználja ezt az erőt és rugalmasságot. Az Regen-nél néha nagy szakítószilárdságú acélt választunk ipari teherbiciklik ahol a végső szilárdság és a sima rugózás a legfontosabb. (Az acél megbocsátó rugózási minősége előnyt jelenthet törékeny rakomány vagy utasok szállítása esetén.) A megfelelő rozsdavédelem (amiről később lesz szó) elengedhetetlen ahhoz, hogy egy acél igásló váz erős maradjon.
- Szénszál: A szénszállal erősített polimer vázakat azért ünneplik, mert könnyű és merev, kiváló szilárdság-tömeg aránnyal. A karbon azonban ritka a teherkerékpárokban – és jó okkal. A karbon vázak nem rendelkeznek kellő rugalmassággal fémből készültek: törés előtt nem hajlanak és nem deformálódnak, egyszerűen csak eltörnek, ha túlterhelik őket. A teherkerékpárokat érő nehéz, változó terhelések alatt a karbon váz hirtelen meghibásodás esetén sebezhető lehet. A karbon ütésállósága is alacsony (egy éles ütés repedést okozhat). Versenykerékpárok esetében a súlycsökkentés kiemelkedő fontosságú, de teherkerékpárok esetében a tartósság és a hosszú távú megbízhatóság még fontosabb. A karbon költsége és a javítás nehézsége tovább korlátozza a használatát ezen a területen. Röviden, bár a karbon teherkerékpár nem lehetetlen, általában nem az optimális választás a tartósság szempontjából. (A karbon és a fém vázak közötti szakértői vitát lásd: BikeRadarútmutató a keretanyagokhoz.)
- Titán és mások: A titánt néha „álomanyagnak” is nevezik – olyan erős, mint az acél, de könnyebb és teljesen rozsdaálló. Léteznek titán teherbiciklik, de rendkívül ritkák a titán... nagyon magas költségek és speciális gyártásNehéz hegeszteni és megmunkálni, ami drága gyártást jelent. Egyedi projektek vagy csúcskategóriás márkák esetében a titánvázak fantasztikus tartósságot kínálhatnak (alapvetően nem korrodálnak, és a kifáradási szilárdságuk hasonló az acéléhoz). A legtöbb teherkerékpár-márka (és flottaüzemeltető) azonban nem olyan árat keres, mint a titán. Egyéb réspiaci anyagok közé tartoznak a laminált falimátumok vagy a bambusz (kompozit erősítéssel), amelyeket egyes kerékpárokban rezgéscsillapításra használnak – érdekes, de nem elterjedt a teherfelhasználásban.
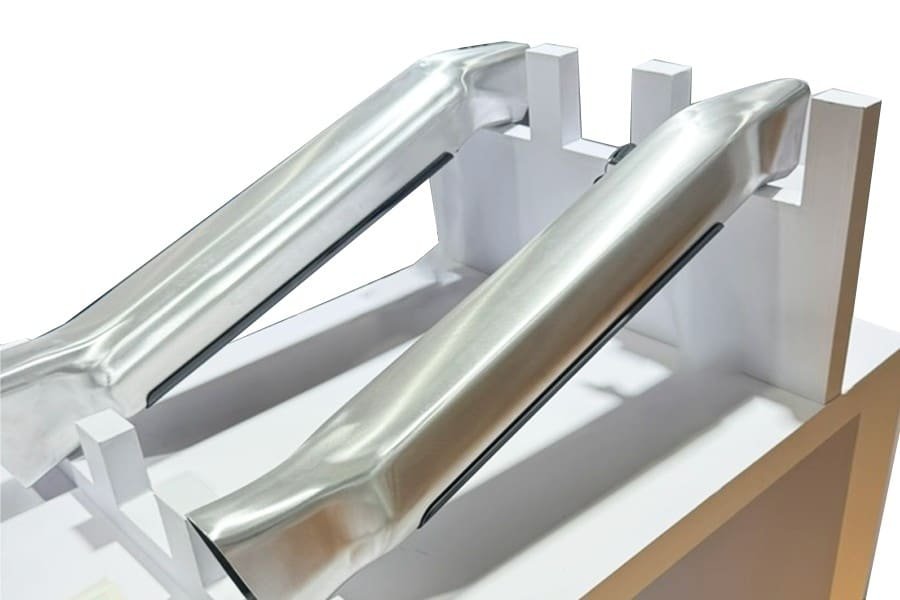
A lényeg: Az alumínium és az acél dominál a teherkerékpár-vázépítésben napjainkban, hogy egyensúlyt teremtsenek az erő, a súly és a költség között. . Az alumínium súlymegtakarítást kínál és nagyon merev, de a tervezésénél figyelembe kell venni a kifáradás csökkentését. Az acél páratlan hosszú távú tartósságot és rugalmasságot kínál, de a plusz súly és a szükséges rozsdavédelem rovására. Az anyagválasztás megalapozza az összes többi tervezési szempontot a tartós váz eléréséhez.
(Kapcsolódó olvasmány: korábbi cikkünk a témában A teherkerékpár teherbírását befolyásoló fő tényezők (kitér arra, hogy a váz anyaga és szerkezete hogyan befolyásolja a kerékpár súlyát.)
Vázgeometria: A forma számít a tartósság szempontjából
Azon túl, amiből a keret készült, a keret formája és szerkezete óriási mértékben befolyásolja az erejét és élettartamát. A geometria nem csak a kezelhetőségről és a rugózási érzetről szól (bár ez is fontos – lásd a bejegyzésünket a Hogyan befolyásolja a vázgeometria a kezelhetőséget? ebből a szempontból); azt is meghatározza, hogyan oszlanak el a feszültségek a keretben.
A kerékpárváz lényegében egy tervezett rácsos szerkezet. A háromszögek a barátaid: A klasszikus rombusz alakú kerékpárváz két egymásba illeszkedő háromszöget használ, mivel ez a forma nem deformálódik könnyen. A teherkerékpárok azonban gyakran eltérnek a rombusz alaktól – lehetnek megnyújtott, hosszú farú kerékpárok vagy elöltöltős kerékpárok. Hosszú Johns raktérrel, vagy akár háromkerekűekkel. Ezek a tervek új geometriai szempontokat vezetnek be a szilárdság megőrzése érdekében:
- Kritikus területek megerősítése: A teherkerékpár vázai gyakran tartalmaznak további csöveket vagy merevítőket a nagy igénybevételnek kitett illesztések megerősítésére. Például egy elöltöltős kerékpár (Long John) jellemzően egy hosszú, meghosszabbított csővel rendelkezik, amely összeköti az első kereket a fő vázzal. Ez a terület háromszögelhető extra rugóstagokkal, hogy megakadályozza a hajlást. Hasonlóképpen, a fejcső (ahol a villa csatlakozik) nagy erőknek van kitéve, különösen nagy terhelés és fékezés esetén. Gyakori, hogy merevítőlemezeket vagy kereszttartókat adnak hozzá a fejcső és a felső cső/alsó cső csatlakozásához, hogy eloszlassák a feszültséget és megakadályozzák a repedéseket. Ezek a tervezési elemek biztosítják, hogy egyetlen cső se viselje önmagában az összes terhelést. Mérnöki szempontból a feszültségkoncentráció csökkentésére törekszünk – ezek meghibásodási kiindulópontok lehetnek, ha nem foglalkozunk velük.
- Teherpálya és súlyeloszlás: A teherbiciklik geometriáját gyakran a rakomány biztonságos szállítására tervezik. alacsony súlypont kívánatos a stabilitás érdekében, ezért az első dobozos kerékpároknál a rakomány alacsonyan, a kerekek között helyezkedik el. A hosszúfarkú kerékpároknál a hátsó háromszög meghosszabbodik, hogy a rakomány vagy az utas súlya a hátsó keréken feküdjön. Mindkét esetben a vázat úgy kell kialakítani, hogy a súly kiegyensúlyozott maradjon, és a rugózás stabil legyen, nélkül gyenge pontok bevezetése. A hosszú vízszintes szakaszokat (például a raktér vagy a meghosszabbított hátsó villák) átlós merevítők támaszthatják meg. Az Regen-nél végeselemes analízist (FEA) alkalmazunk a tervezés során, hogy szimuláljuk, hogyan viselik a különböző vázformák a terhelést, a geometriát finomhangolva az optimális egyensúly érdekében a szilárdság és a súly között. Például az RS01-esünk raktérváza egy gondosan megtervezett rácsos szerkezet, amely akár 250 kg-ot is elbír túlzott rugalmasság nélkül, miközben a kerékpár tömegközéppontja alacsonyan marad.
- Speciális teherbicikli-kialakítások: Minden teherkerékpár-geometria típusnak megvannak a maga tartóssági előnyei és hátrányai. Hosszú János (első dobozos kerékpár) gyakran robusztus kormányösszekötővel és meghosszabbított vázzal rendelkezik – több ízülettel és alkatrésszel, de általában kiegyensúlyozott terheléselosztással is. Hosszúfarkú inkább egy átlagos kerékpárra hasonlít, de megnyújtva; sok súly koncentrálódhat a hátsó kerékre és a felső villákra, ami erős hegesztési varratokat és esetleg vastagabb csöveket igényel. háromkerekű tehertrike eredendően széles és stabil alapterülettel rendelkezik, de a váza torziós (csavarodásos) sérülést szenvedhet kanyarodáskor, ha az egyik kerék felemelkedik, vagy egyenetlen talajon halad. Ezért a tricikli vázai néha további keresztgerendákkal rendelkeznek, hogy merevítsék őket az elcsavarodás ellen. Minden geometria (középső farú, kerékpártartó stb.) átgondolt szerkezeti tervezést igényel, hogy elkerüljük a terhelés alatti hajlást vagy meghibásodást.
Szemléltetésképpen vegyük figyelembe a Babboe teherbicikli visszahívás ami híreket hozott az iparágban: a vázproblémáikat részben olyan tervezési döntéseknek tulajdonították, amelyek nem kezelték megfelelően a valós terheléseket. Néhány váz megrepedt az alsó csőnél a tervezési és hegesztési problémák kombinációja miatt. Ez rávilágít arra, hogy még egy erős anyaggal is, A rossz szerkezeti geometria vagy a nem megfelelő megerősítés tartóssági problémákhoz vezethet. Ezeket a tanulságokat szívünkre vesszük a saját terveink kidolgozásakor.
Összefoglalva, egy tartós teherkerékpár váz erős formára alakítvaA háromszögek, ívek és merevítők stratégiai használata megerősíti a szerkezetet. A geometriának meg kell egyeznie a tervezett felhasználással – egy nehéz terhelések szállítására épített váz például tartalmazhat egy ívelt felső csövet a könnyebb áthaladás érdekében, de egy extra alsó csővel van megerősítve a szilárdság érdekében. A váztervezésben egyszerre van művészet és tudomány: művészet a praktikus forma megalkotásában, tudomány pedig abban, hogy biztosítsuk, hogy a forma kiállja az idő próbáját. (A különböző teherkerékpár-vázelrendezésekről és azok jellemzőiről bővebben a magyarázó cikkünkben olvashat.) Különböző típusú teherkerékpár-vázak a Teherkerékpár-szószedet sorozat.)
Hegesztések és illesztések integritása: Erős kapcsolat létrehozása
Még a legjobb anyagokat és geometriát is alááshatja egy dolog: gyenge hegesztések vagy illesztések. A csövek összeillesztési (hegesztési vagy forrasztási) pontjai jellemzően a legnagyobb stressz zónák egy vázban. Nem meglepő, hogy sok vázhiba hegesztési varratoknál vagy a hegesztés melletti hőhatásövezet környékén keletkezik. Egy nehéz terhet szállító tehermotor esetében a hegesztés épségének biztosítása elengedhetetlen.
Az Regen-nél gyakran mondjuk, hogy a váz csak annyira erős, mint a leggyengébb hegesztési varrata. Mi kell egy erős kötéshez?
- Minőségi hegesztési technikák: A legtöbb fém teherkerékpár váz TIG (volfrám inert gázzal) vagy MIG hegesztést használ a csövek összeolvasztásához. A TIG hegesztés, amelyet képzett kéz vagy precíziós robotrendszer végez, lehetővé teszi a finom szabályozást, hogy erős, egyenletes varratokat hozzon létre. A cél a hegesztés teljes behatolása (ami azt jelenti, hogy a hegesztési varrat teljesen átolvad az alapanyaggal való illesztésen) hibák nélkül. Az alumínium vázgyártás során bevett gyakorlat a teljes váz hőkezelése hegesztés után (T6-os hőfokra való visszaállítás), mert a hegesztési hő meglágyíthatja az alumíniumot ezen a területen. Ennek a lépésnek a kihagyása gyengítheti a hegesztési zónát. AcélkeretbenAz olyan technikák, mint a forrasztás (fülekkel) vagy a TIG-hegesztés, egyaránt működhetnek – a TIG-hegesztett kötések szükség esetén kisebb merevítésekkel megerősíthetők. A lényeg, hogy a hegesztési varratban ne legyenek repedések, üregek vagy zárványok.
- Hegesztések ellenőrzése és tesztelése: Gyárainkban minden keret hegesztését vizuálisan ellenőrizzük, és gyakran roncsolásmentesen teszteltA festékpenetrációs vizsgálat például mikrorepedéseket képes feltárni a hegesztési varratokban – a vizsgáló speciális festéket és előhívót alkalmaz, hogy kiemelje a szabad szemmel láthatatlan apró hibákat. A csúcskategóriás vázgyártók (különösen a kritikus elektromos kerékpár vázak esetében) akár röntgenes vagy ultrahangos vizsgálatot is végezhetnek a hegesztéseken, hasonlóan a repülőgépipari szabványokhoz. Ez a minőségellenőrzési szint biztosítja, hogy a rejtett hibák ne csúszhassanak át. Ez a fajta szorgalom akadályozza meg, hogy egy apró repedés később nagy hibává váljon.
- Az illesztés kialakítása: Néhány illesztés eleve robusztusabb, mint mások. Például, kettős nyírókötések (ahol egy cső két lemez vagy fül között átfedésben van) erősebb lehet, mint egy tompa illesztés. A tehergépkocsiknál gyakran látni erősítőhüvelyeket vagy gallérokat a nagy igénybevételnek kitett illesztések körül, mint például a fejcső vagy a nyeregcső-csoport. Ezek a hüvelyek elosztják a terhelést és csökkentik a hegesztés feszültségét. Egy másik technika a halszájformálás csővégek – a cső kontúrja úgy van kialakítva, hogy hegesztés esetén tökéletesen illeszkedjen az illeszkedő csőhöz, maximalizálva az érintkezési felületet. Ezeket a részleteket beépítjük a keretkialakításainkba, hogy biztosítsuk a hegesztések túlterhelésének elkerülését. Ezenkívül a sima, folyamatos hegesztési varratok (a szakaszos hegesztés helyett) segíthet kiküszöbölni a feszültségnövekedéseket. Egy jól kivitelezett hegesztésnek úgy kell kinéznie, mint egy rendezett érmeköteg, amely egyenletesen burkolja a kötést.
Miért fontos mindez? Vegyük például a korábban említett sajnálatos esetet: egy nagy márkának vissza kellett hívnia a kerékpárokat a következők miatt: „Nem megfelelő hegesztési és tervezési hibák”, amelyek nyomás alatti kerethibákhoz vezetnek . Ebben az esetben valószínűleg néhány hegesztés hibás volt, vagy a csatlakozások kialakítása nem volt megfelelő, ami repedéseket okozott, amikor a kerékpárosok felpakolták a kerékpárt. A tanulság világos – a hanyag hegesztés nem lehetséges, ha a biztonság forog kockán. Ezért az Regen kínai gyártópartnerei szigorú hegesztési eljárásokat követnek (az ISO és EN szabványokkal összhangban), és portugáliai összeszerelő üzemünk minden tételen végső minőségellenőrzést végez.
Röviden, erős, tiszta hegesztések = tartós keretekFáradságos munka – szakértelmet, megfelelő felszerelést és a minőségbiztosítás terén sem lehet gyors megoldást találni. De ez a befektetés megtérül, mivel gyakorlatilag kiküszöböli a kerékpárvázak egyik gyakori meghibásodási pontját. Legközelebb, amikor teherbiciklit nézel, ellenőrizd a hegesztési varratokat: ezek sokat elárulhatnak a váz építési minőségéről.
Fáradtság- és stresszteszt: Az erő időbeli érvényesítése
Egy erős váz megtervezése és építése egy dolog – bizonyítás A tartóssága egy másik fontos tényező. Itt jön képbe a szigorú fáradási és terhelési teszt. Vázainkat szimulált laboratóriumi teszteknek és valós körülmények között végzett próbáknak is alávetjük, hogy megbizonyosodjunk arról, hogy képesek ellenállni a teherkerékpározás ismétlődő terheléseinek és alkalmankénti rázkódásának hosszú éveken keresztül. Nézzük meg, hogyan működik a váztesztelés, és miért létfontosságú.
Laboratóriumi fáradásvizsgálat: Laboratóriumi tesztek során a vázat szerelvényekbe szerelik, és szabályozott erőhatásoknak teszik ki, amelyek pedálozást, fékezést és rázkódásokat szimulálnak, ezerszer és ezerszer megismételve. Például egy gyakori teszt egy pedálfáradási teszt – a vázat a hátsó villapapucsoknál rögzítik, és ciklikus terhelést alkalmaznak ott, ahol a középcsapágy/lánc lenne, utánozva a kemény pedálozás erőit. Egy másik lehetőség a fejcső fáradási teszt, ahol az erők elcsavarják a villát/első részt, mintha egyenetlenségeknek ütközne, vagy a kerékpáros a kormányon birkózik. Iparági szabványok, mint például ISO 4210-6 (kerékpárvázakhoz) és az újabb, rakományspecifikus DIN 79010 (2020) Adja meg az ilyen típusú teszteket meghatározott terhelésekkel és ciklusszámokkal. A sikeres teljesítéshez egy keretnek túl kell élnie, például 100 000 terhelési ciklus repedések kialakulása nélkül.
A teherkerékpárokra vonatkozó szabványok még magasabbra teszik a lécet. A német DIN 79010 és a hamarosan megjelenő európai EN 17860 szabványok elismerik, hogy a teherkerékpárok... nagyobb feszültségek mint a normál kerékpárok. Következésképpen a tesztterhelések nagyobbak, és további teszteket is végeznek (például az utasok szállítására vonatkozó kapacitás vizsgálatát). Sok gyártó (beleértve minket is) független tanúsítványt kér ezeknek a szabványoknak megfelelően. Például tesztlaboratóriumokkal működünk együtt, hogy elvégezzük a vázaink teljes tesztsorozatát. Bizonyos esetekben még a szabványon is túllépünk: a vázakat addig futtatjuk, amíg... kudarc hogy lássuk, mennyi igénybevételt bírnak ki. Ez a „pusztító teszt” megközelítés segít azonosítani a leggyengébb láncszemet, és biztonsági ráhagyást biztosít a normál használaton túl. (Egy teherkerékpár-gyártó, a Tern megjegyezte, hogy egyes vázaik annyira robusztusak voltak, hogy a laboratóriumi gépeket le kellett állítani, mert a váz nem tenné szünet – az alapos mérnöki munka bizonyítéka.)
A szélsőséges kerettesztelés egyik nagyszerű példája a EFBE Tri-Test® Németországban kifejlesztett protokoll. Ez egy kifejezetten teherkerékpár-vázakra vonatkozó kínzóteszt, amely messze túlmutat az alapvető szabványokon. A Tri-Test során a váz és a villa több irányból végzett fáradási, maximális terhelési és túlterhelési teszteken megy keresztül. A vázakat több százezer terhelési ciklusnak tehetik ki különböző szögekből – ez egy teljes élettartamot szimulál tömör formában. Valójában a Tri-Test részeként a vázak nagyságrendileg... 100 000 ismétlődő ciklus nagy terhelés alatt, külön ütéstesztekkel kombinálva. Azzal, hogy a váz kiállta ezt a próbát, tanúsítványt kap arról, hogy valóban alkalmas a valós teherszállításra. Saját terveink tesztelésekor is ezekből a szigorú protokollokból merítünk ihletet (még ha nem is minden váz kapja meg a hivatalos EFBE tesztet, a filozófia ugyanaz: feszegetni a határokat, és még annál is többet).
Statikus terhelés- és ütésvizsgálat: Az ismételt fárasztó ciklusokon kívül a tartóssági vizsgálatok statikus terheléses vizsgálatokat (fokozatos nagy terhelés alkalmazása annak megállapítására, hogy a váz enged vagy deformálódik-e) és ütésvizsgálatokat (súly leejtése a vázra vagy meghatározott pontokon való ütése ütközés vagy járdaszegélynek ütközés szimulálására) is tartalmaznak. Erre példa a keretesés-teszt: egy súlyozott tömeget ejtenek egy keretre, vagy a keretet egy bizonyos magasságból ejtik le, hogy ellenőrizzék, nem reped-e meg. Egy másik a túlterhelési teszt: a névleges kapacitásnál lényegesen nagyobb súlyt helyeznek a raktérre a biztonsági puffer biztosítása érdekében. Ezek a tesztek nemcsak az azonnali törést, hanem az esetleges egyéb sérüléseket is ellenőrzik. maradó deformáció – egy tartós váznak vissza kell pattannia és egyenesen kell maradnia, ha az ütközés a várható forgatókönyveken belül történik. Az olyan szabványok, mint az EN 17860, felvázolják ezeket a teszteket, hogy a vázak megfeleljenek a biztonsági követelményeknek, mielőtt eljutnának a fogyasztókhoz.
Valós tesztelés: A laboratóriumi tesztek elengedhetetlenek, de hiszünk a jó öreg közúti tesztekben is. Mielőtt véglegesítenénk a váztervét, prototípus kerékpárokat építünk, és keményen vezeted őket valós körülmények között – macskakövek, kátyúk, tele rakománnyal, meredek emelkedők, hirtelen fékek, nevezd meg, amit csak szeretnél. Ez a tapasztalati tesztelés gyakran olyan problémákat tár fel, amelyeket egy laboratórium nem feltétlenül észlel (vagy megerősíti, hogy a laboratóriumi szimulációk pontosak voltak). Például egy váz kiválóan teljesítheti a laboratóriumi fáradási teszteket, de ha sokféle kerékpáros használja, egy hónapnyi futárszolgálat után váratlan rugalmasságot fedezhetünk fel a raktérben, vagy enyhe lazulást egy illesztésben. Ez a visszacsatolási hurok lehetővé teszi számunkra, hogy finomítsuk a hegesztési folyamatokat, vagy megerősítést adjunk hozzá a tömeggyártás előtt. Sok vezető gyártó végez hasonló kísérleti tesztelést – arra ösztönözve a munkatársakat vagy a béta tesztelőket, hogy komoly futásteljesítményt mérjenek az új modelleken. Nem ritka, hogy mérnökeink homokzsákokkal pakolnak meg egy teherbírású kerékpárt, és ismételten fel-le másznak egy tesztdombon a létesítményünk közelében, próbálva terhelés alá helyezni a fékeket és a vázat. A mottó itt az, hogy „érvényesít, érvényesít, érvényesít.”
Amikor egy váz minden teszten – laboratóriumban és terepen egyaránt – átmegy, magabiztosan állíthatjuk, hogy tartós. Ezt követően erős garanciákat vállalunk rá. (Az Regen többéves vázgaranciát és robusztus értékesítés utáni támogatást kínál a...) Szolgáltató központ (Mert termékeinket teszteltük, hogy tudjuk, tartósak. Ha bármilyen probléma merül fel az ügyfelek általi használat során, elemezzük, és ezt a tudást felhasználjuk a következő tervjavítás során.)
És mint mindig, bátran forduljon hozzánk az Regen címen, ha konkrét kérdései vannak, vagy olyan ODM partnerre van szüksége, aki a teherkerékpárok tartósságát éli és lélegzi.
Összefoglalva, a fáradás- és stressztesztelés az, ahol a mérnöki munka találkozik a valósággalEz egy kulcsfontosságú lépés annak biztosítására, hogy az elméleti szilárdság számtalan túrán át kitartson. Ha teherkerékpár-beszállítókat értékelsz, bölcs dolog megkérdezni: a vonatkozó szabványoknak megfelelően tesztelik-e őket? Túlteljesítik-e a minimális követelményeket? Egy tartós váz nem csak úgy megszületik; igazolt ilyen szigorú vizsgákon keresztül, így a motorosok és a flottaüzemeltetők megnyugodhatnak afelől, hogy ezek a motorok nem fognak megingni, ha nehéz helyzetbe kerülünk.
Korrózióvédelem: Harc az elemekkel a hosszú élettartamért
Képzelj el két egyforma acél teherbicikli vázat: az egyik egy éven belül rozsdásodni kezd, és végül a kritikus illesztéseknél meggyengül; a másik pedig ellenáll az esőnek és az útsónak, és évek múlva is úgy néz ki és úgy működik, mint az új. Mi a különbség? Korrózióvédelem. A váz tartósságának egyik hatalmas tényezője, hogy mennyire védett az elemek ellen – a víz, a só és még az UV-sugárzás is idővel lebonthatja az anyagokat. Ez különösen fontos az acélvázak esetében (amelyek rozsdásodhatnak), de az alumínium esetében is fontos (amelyek korrodálódhatnak, bár másképp), valamint a festék és a matricák tartóssága szempontjából.
Az Regen-nél a korrózióvédelmet ugyanolyan fontosnak tartjuk, mint a szerkezeti tervezést. Megközelítésünk jellemzően többrétegű bevonatolási eljárást foglal magában, ahol a főszereplő a ED-bevonat (elektroforetikus leválasztásos bevonat), más néven e-bevonatolás. Íme, mit csinálunk és miért fontos:
- ED bevonat alapozó: Az ED-bevonat egy fejlett festési technika, amelyet az autóiparból kölcsönöztek. Röviden, a vázat egy speciális, elektromosan töltött festékfürdőbe mártják, ami egyenletes, hihetetlenül tapadó bevonatot hoz létre minden felületen, kívül-belül. Képzelje el úgy, mint egy rozsdagátló alapozót, amely még a váz rejtett zugait is eléri – csőfalak belsejét, hegesztési repedéseket stb., ahol a festékszóró vagy a porfesték esetleg nem fedne le teljesen. Ez azért kulcsfontosságú, mert a rozsda gyakran láthatatlan helyeken kezdődik (például egy cső belsejében vagy egy konzol alatt), majd kifelé kúszik. Az ED bevonattal ezek a belső felületek védőréteget kapnak. Az eredmény egy olyan keret, amely rendkívül zord körülményeknek is ellenáll. Valójában a katódos ED bevonatok (az általunk használt típus) könnyen átmennek rajta. Több mint 1000 óra sópermet-tesztelés korrózió jelei nélkül – autóipari szintű teljesítmény. Hogy ezt perspektívába helyezzük, 1000 óra sóködkamrában sokkal nagyobb igénybevételnek van kitéve, mint amennyit egy kerékpár évekig tartó tengerparti vagy téli kerékpározás során kibírna. Ez jó prediktív válasz arra a kérdésre, hogy „el fog-e rozsdásodni ez a váz?”, és az ED bevonattal a válasz nem.
- Porbevonat és festék: Az ED alapozó tetejére általában egy tartós porfesték színért és további vastagságért. A porfestés során elektrosztatikusan felvisznek egy száraz port, majd beégetik, így egy erős festékréteget képezve. Jobban ellenáll a lepattogzásnak és a karcolásoknak, mint a hagyományos nedves festék. Ez az elsődleges színréteg. Végül egy átlátszó lakk vagy lakk alkalmazható UV-védelem és fényesség érdekében. Ezen rétegek mindegyike hozzájárul a korrózióállósághoz – ha a fedőréteg lepattogzik, az alatta lévő ED bevonat továbbra is távol tartja a rozsdát az acélvázon (és az alumínium, bár nem „rozsdásodik”, oxidálódhat és gyengítheti az illesztéseket, ha nincs védve, így a bevonat ezt az oxidációt is megakadályozza). Portugáliai létesítményünk a legmodernebb festési képességekkel rendelkezik (az egyik oka annak, hogy az EU-ban szereljük össze és fejezzük be a vázakat, az az, hogy szigorú minőséget biztosítsunk ezeknél a befejező lépéseknél). Egyedi felületeket is kínálunk – például az ügyfelek választhatnak egyedi RAL színeket, vagy akár horganyzást is speciális felhasználású kerékpárokhoz –, de mi... soha ne hagyd ki a korróziógátló alaprétegeket.
- Rozsdamentes acél szerelvények és vízelvezetés: A festésen túl más tervezési megoldások is védenek a korrózió ellen. Ahol csak lehetséges, rozsdamentes acél csavarokat és rögzítőelemeket használunk, hogy a vázhoz csavarozott kiegészítők vagy tartók ne váljanak a rozsda kialakulásának helyévé. A vázakat szükség esetén vízelvezető nyílásokkal vagy szellőztetővel is ellátjuk – ha víz kerül a vázcsőbe (esőből vagy mosásból), az kiszáradhat, ahelyett, hogy tócsába gyűlne. Az ilyen apró részletek segítenek biztosítani, hogy a nedvesség ne csapdába essen a fémen. Az alumínium vázak esetében odafigyelünk a következőkre: galvánkorrózió (amikor az alumínium elektrolit jelenlétében érintkezik az acéllal, korrodálódhat) – a különböző fémeket szigetelő alátétekkel vagy bevonatokkal választják el egymástól az ilyen reakciók megelőzése érdekében.
Miért vesződne ennyi bajjal? Mert egy vázszerkezetet szerkezetileg túl lehet építeni, és soha nem reped meg a feszültségtől, mégis idő előtt meghibásodhat, mert belülről rozsdásodott – egy csendes gyilkos. Láttunk már olyan eseteket a terepen (különösen az olcsóbb, kint hagyott tehermotorok esetében), amikor néhány téli időszak után a festék felhólyagosodott a hegesztések körül, és narancssárga rozsda kezdett lehúzódni. Ez annak a jele, hogy a váz védőrétegei megsérültek, és a korrózió megtelepedett benne. Idővel a rozsda beleharaphat a hegesztési varratba, vagy elvékonyíthatja a cső falát, jelentősen csökkentve a szilárdságot. Az olyan robusztus korrózióvédelemmel, mint az ED bevonat, ez a forgatókönyv gyakorlatilag kiküszöbölhető – egy jól bevont váz legrosszabb esetben is csak némi esztétikai felületi rozsdát kaphat, ha mélyen megkarcolódik, de belsőleg semmilyen szerkezetileg érdemi módon nem korrodálódik.
Ezenkívül a vázfelület megőrzése azt jelenti, hogy a kerékpár hosszabb ideig jobban néz ki, ami fontos ügyfeleink arculata szempontjából (senki sem akarja, hogy a szállítóflottája úgy nézzen ki, mint a kerekeken guruló tetanusz). Biztonsági és karbantartási előny is: az alkatrészek kisebb valószínűséggel szorulnak be vagy fagynak be rozsda miatt. A mi... Egyedi festés és Matricák/Logó A lehetőségek mind a védőburkolat megőrzésének keretein belül működnek – gondoskodunk arról, hogy az egyedi grafika vagy logófelvitel ne veszélyeztesse az alatta lévő bevonatokat.
Összefoglalva, Egy tartós váznak nemcsak a fizikai, hanem a környezeti terheléseknek is ellen kell állniaA legkiválóbb korróziógátló eljárások, mint például az ED bevonat és a minőségi kidolgozás alkalmazásával lényegében „páncélozzuk” meg vázainkat az elemek ellen. Így évek múltán egy teherkerékpár élettartamát korlátozó tényező az, hogy mennyi munkát végzett – nem kúszó rozsda vagy kopott festék. (Az ED bevonatról és annak előnyeiről részletesen olvashat blogbejegyzésünkben.)ED bevonat: Elektromos kerékpárok és teherkerékpárok vázának védelme hosszú utakon„ahol elmagyarázzuk a mögötte álló tudományos hátteret, és azt, hogy miért forradalmi változást hoz a tartósság terén.”
Gyártási pontosság: Tűrések és minőségellenőrzés
A tartósságról beszélve gyakran a nagyobb tényezőkre, például az anyagokra és a tesztelésre összpontosítunk. Ugyanilyen fontosak azonban a a gyártási pontosság és a minőségellenőrzés „apró” részletei. Egy teherbicikli váza nem csupán összeragasztott fémből áll – egy gondosan illesztett szerkezet, ahol a milliméterek is számítanak. A gyártás során fellépő apró egyenetlenségek feszültségnövelőket vagy gyenge pontokat okozhatnak, amelyek csak sokkal később jelentkeznek. Ezért hangsúlyozzuk az Regen-nél a szigorú gyártási tűréshatárokat és az alapos minőségellenőrzést a teljes építési folyamat során.
Igazítás és tűrések: A vázgyártás során kritikus fontosságú az összes cső megfelelő beállításának fenntartása. Ha a vázsablon (a csöveket hegesztéskor rögzítő szerelvény) akár csak kicsit is el van tolva, akkor a váz rosszul illeszkedhet – talán a hátsó villapapucsok nem tökéletesen szimmetrikusak, vagy a fejcső egy fokkal eltér a specifikációtól. Az eltolódás lehetővé teheti a kerékpár összeszerelését és használatát, de ez azt jelentheti, hogy terhelés alatt a váz egyik oldala nagyobb terhelést visel, mint a másik. Idővel ez az egyensúlyhiány kifáradásos repedésekhez vezethet a túlterhelt oldalon. Ezért szigorú tűréshatárokat határozunk meg: például a villapapucsok beállítása <1 mm-en belül, a fejcső és a nyeregcső párhuzamossága egy fok töredékén belül, a középcsapágyház felületei pedig laposra és párhuzamosan megmunkálva. Sok jó hírű kerékpárgyártó hasonló értékekre törekszik (a kritikus méretekben 0,5–1 mm-es tűréshatár nagyságrendben). Ennek eléréséhez precíziós szerelvényekre, képzett hegesztőkre (mivel a hegesztési hő hűlés közben eltorzíthatja az illeszkedést), és gyakran hegesztés utáni... hidegen kötő vagy megmunkálás. Hegesztés és hőkezelés után rutinszerűen ellenőrizzük a kereteket egy síkasztalon, illesztőidomszerekkel. Bármely, a specifikációtól eltérő keretet finoman beállíthatunk, vagy ha túl nagy az eltérés, elutasíthatjuk. Ez a pontossági szint biztosítja, hogy minden általunk szállított keret szerkezetileg egyenes és pontos legyen, így az erők a terv szerint áramlanak rajtuk keresztül.
A stresszkeltők elkerülése: A „feszültségnövekedés” az anyag vagy a geometria hirtelen változása, amely a feszültséget koncentrálja (például egy éles sarok vagy egy nem megfelelő köszörülés). A gyártás során kerüljük a nem kívánt feszültségnövekedések létrehozását. Például, amikor apró alkatrészeket, például konzolokat vagy kábelütközőket hegesztünk, ügyelünk arra, hogy úgy legyenek elhelyezve, hogy ne okozzanak feszültségkoncentrációt a fő csöveken. Ha egy hegesztési varrat a cső felületén végződik, simán kúposítjuk és köszörüljük, hogy illeszkedjen a csőhöz. Ha furatra van szükség (például a kábelek belső vezetéséhez vagy a csavarok rögzítéséhez), megerősítjük ezt a területet, vagy gyűrűket használunk, hogy a furat ne váljon repedéskialakulási hellyé. Ezek a gyakorlatok a gyártási know-how részét képezik, amelyek megkülönböztetik a tartós vázat egy átlagostól. Egy anekdota: a gyártásunk elején egy prototípuson egy adott állványtartó közelében hajszálrepedés-hajlamot észleltünk extrém tesztelés után. Megállapítottuk, hogy az adott tartó hegesztési varrata egy olyan helyen végződött, ahol hajlott. A megoldásunk az volt, hogy a hegesztési varratot tovább kiterjesztettük, hogy egy alacsony feszültségű régióban végződjön, valamint hogy a tartó alapjának sugarát is nagyon kis mértékben megnöveltük a terhelés elosztása érdekében. Az eredmény – nincsenek többé repedések. Az ilyen iteratív finomítás és a mikrorészletekre való odafigyelés csak szigorú minőségellenőrzési visszacsatolási ciklussal lehetséges.
Minőségellenőrzési pontok: A gyártás során számos minőségellenőrzési pont segít a problémák kiszűrésében. Már említettük a hegesztési varratok és az illesztések ellenőrzését. Ezenkívül az anyagellenőrzést (annak biztosítására, hogy a használt ötvözet pontosan megfeleljen a specifikációnak – pl. eredeti 6061 ötvözetű cső, és nem egy olcsóbb helyettesítő) a beszállítóktól származó anyagtanúsítványok és néha szúrópróbaszerű vizsgálatok segítségével végezzük. Felületkezelési ellenőrzéseket is végzünk: a váz teljes felületét a bevonás után ellenőrizzük, hogy nincsenek-e lyukak vagy fedési rések a festékben, amelyek később korróziót okozhatnak. Portugáliai összeszerelő csapatunk véletlenszerűen kiválasztott vázakból készíti el a végső összeállítást, hogy megbizonyosodjon arról, hogy minden tökéletesen illeszkedik – ha egy vázon rosszul elhelyezett dudor vagy enyhe torzulás van, azt az alkatrészek beszerelésekor észreveheti. Ez az átfogó minőségellenőrzési folyamat a megbízható OEM-nek számít. Ahogy egy iparági szakértő találóan megjegyezte, megfelelő minőségellenőrzéssel és felügyelettel a gyártási eltérések szigorúan ellenőrizhetők, és nagyfokú állandóság érhető el, függetlenül a gyártási helytől. Más szóval, az Ön által érvényesített rendszerek és szabványok határozzák meg a minőséget. Együttműködünk a vázgyárunkkal a megvalósításban. ISO 9001 tanúsítvánnyal rendelkező folyamatok és folyamatosan figyelemmel kísérjük a gyártási folyamatokat. A cél az, hogy minden egyes, a gyártósorról legördülő képkocka olyan jó legyen, mint az elsőként jóváhagyott termék.
Gyártási tűrések a gyakorlatban: Mit jelent mindez a tartósság szempontjából? Azt jelenti, hogy minden vázat a mérnökök elképzelései szerint építenek. A megfelelően elhelyezett középcsapágy-házak megakadályozzák a csapágyakra nehezedő terhelést (ha egy középcsapágy nem derékszögű, az terhelést jelenthet a házra vagy a hajtótengelyre). A jól beállított villapapucsok azt jelentik, hogy a hátsó kerék egyenesen ül, így a bal/jobb terhelés kiegyensúlyozott. A középre helyezett fejcső azt jelenti, hogy a villa nem nyomódik finoman az egyik oldalra, ami egyébként aszimmetrikus terhelést okozhatna az alsó csőben. Ezek az apró tényezők idővel megőrzik a váz integritását. Ezenkívül a precíziós gyártás biztosítja, hogy a kerékpár kiszámíthatóan kezelhető legyen (ami közvetve a tartósságot is befolyásolja – a kevesebb billegés és hajlás kisebb esélyt jelent a szokatlan terhelésekre vagy ütközésekre).
A gyártásban szeretjük azt mondani, hogy „nulla hiba” a cél. Bár a tökéletesség egy utazás, nem pedig egy végállomás, a rá való törekvéssel drasztikusan csökkentjük annak esélyét, hogy egy rejtett hiba lerövidítse a váz élettartamát. Ezért fektetünk be képzett kézművesekbe, megfelelő felszerelésekbe és alapos képzésbe mind a kínai vázgyárunkban, mind a portugáliai összeszerelő üzemünkben. Ez utóbbi, egy 49 000 m²-es, korszerű gyár Águedában, Portugáliában, lehetővé teszi számunkra, hogy a végső hangolást és összeszerelést Európában végezzük, ami egy extra minőségellenőrzési réteget biztosít, és biztosítja az EU-s szabványoknak való megfelelést közvetlenül a kontinensen. A hatékony gyártás és az aprólékos kidolgozás ezen ötvözete az, ahogyan tartós vázakat szállítunk nagy mennyiségben.
(A kulisszák mögé bepillantásért látogasson el a mi… Az Regen-ről oldalunk részletesen ismerteti a teljes gyártási megközelítésünket, beleértve azt is, hogy a kínai székhelyű vázgyártásunk és a portugáliai összeszerelésünk hogyan működik együtt a kiváló minőség elérése érdekében. És ha érdekli a váz specifikációinak vagy jellemzőinek testreszabása a szigorú tűréshatárok betartása mellett, tekintse meg a következő oldalunkat: Egyéni funkcionális konfiguráció szolgáltatások – a terveket az Ön igényeihez igazíthatjuk anélkül, hogy feláldoznánk minőségbiztosítási szabványainkat.)
Valós teljesítmény: Terhelésdinamika és használatra gyakorolt hatás
Végül beszéljünk a váz tartósságának végső bizonyító pályájáról: valós használat. Egy teherbicikli váza nap mint nap dinamikus erőhatásoknak van kitéve: elindulások és megállások, kanyarokban fellépő terhelések, rázkódások, sőt, talán még az alkalmankénti felborulás is. Az, hogy a váz hogyan bírja ezeket az évek során, a tartósság igazi mércéje. Ez nagyrészt a már tárgyalt tényezők (anyag, kialakítás, hegesztések stb.) összessége, de érdemes konkrétan megvizsgálni, hogyan... terhelésdinamika és felhasználói viselkedés befolyásolják a váz élettartamát – és hogyan vesszük ezeket figyelembe a terveinkben.
Dinamikus vs. statikus terhelések: Egy váz gond nélkül elbír egy statikus súlyt (mondjuk egy 200 kg-os, mozdulatlan teher). Az igazi próbatétel az, amikor ez a súly mozgásban van. Dinamikus terhelések Ide tartozik a súlyeltolódás fékezés közben (erős fékezéskor a rakomány tehetetlensége extra erőt fejt ki a váz elejére), az oldalirányú erők kanyarodáskor (a váz kissé oldalra hajolhat egy hirtelen kanyarodáskor), és a függőleges lökésszerű terhelések (kátyúba csapódás vagy a járdaszegélyről való lehajtás teherrel erőcsökkenő hatást kelt). Ezek a dinamikus események rövid időre messze meghaladhatják a rakomány statikus súlyát. Például egy 100 kg-os rakomány, amely nagy sebességgel egy buckának csapódik, több G-s effektív erőt fejthet ki – a váz pillanatnyilag úgy érzi, mintha 200–300 kg-ot cipelne ebben a rázkódásban. Egy tartós vázat úgy kell megtervezni, hogy legyen tartaléka ezen ütések elnyelésére. Ezért nem elég pusztán a „névleges teherbírás” vizsgálata; a beépített biztonsági tényezőkről is szól. Az Regen-nél ilyen eseményeket szimulálunk végeselemes analízissel (FEA), és kínzótesztekkel validáljuk a kerékpárokat hirtelen súlyesésekkel és vészfékezésekkel. A kritikus illesztéseket (például a fejcső/alsócső kereszteződését és a villakoronát a kerékpárjainkon) úgy tervezzük, hogy... fékező terhelések jóval meghaladja a normál használattal járó terhet. Végül is egy teherbringa könnyedén nyomhat 40+ kg-ot, adjunk hozzá egy kerékpárost (80 kg) és a rakományt (mondjuk 100 kg), ami nagy sebességnél 220+ kg – a vázra és a villára ható fékerők hatalmasak. Biztosítjuk, hogy a váz fejcső területe és a villa illesztése ezt elbírja görbülés vagy repedés nélkül (a megfelelő, nagy szilárdságú villák kiválasztásával párosítva). Fékezőerők különösen nagy terhelést jelentenek a váz elülső részének; egy rosszul megtervezett váz repedések keletkezhetnek a fejcső közelében, ha az anyag vagy a hegesztések nem elég erősek. (Megjegyzés: ez az egyik oka annak, hogy a tehergépkocsikon az erős fékrendszereket, például a hidraulikus tárcsákat javasoljuk. Nemcsak a féktávolság javul, hanem simábban modulálják az erőket is. A nagy terhelés alatt túlmelegedő mechanikus fékek elhalványulhatnak, arra kényszerítve a kerékpárosokat, hogy erősebben húzzanak, és potenciálisan hirtelen erőhatásokkal terheljék a vázat. A váz tartóssága és a fékteljesítmény ilyen módon összekapcsolható.)
Teher elhelyezése és vázszerkezet: A rakomány elhelyezése és elhelyezése befolyásolhatja a váz terhelését. Az első dobozban lévő rakomány közvetlenül a kerekek között általában kíméletesebb a vázszerkezet számára (a rakomány jobban központosul), mint ugyanaz a súly, amely a hátsó csomagtartón lóg, és ezáltal emelőerőt hoz létre. Ezért a különböző vázkialakításoknak néha eltérő a teherbírásuk elöl és hátul. A mi RS01-esünket például a raktérben lévő első rakományhoz optimalizáltuk, a súlyt a kormánytengely közelében és alacsonyan a talajhoz helyezve – ez jobb kezelhetőséget eredményez, és azt is jelenti, hogy a vázat nem terheli annyira a lengő teher. A kézikönyveinkben a megfelelő rakodásra tanácsoljuk a felhasználókat (tartsa kiegyensúlyozottan, rögzítse hevederekkel az elmozdulás elkerülése érdekében). Egy tartós váz elbír némi helytelen használatot, de a legjobb gyakorlat tovább meghosszabbítja az élettartamát. A motoros súlya és viselkedése Ez is számít: egy nehéz kerékpáros állva és pedálozva nagy terhelést jelenthet a középcsapágy és a láncvillák számára (csavaró erők, ahogy oldalra billegnek). Ezt figyelembe veszik a tesztelés során (pedálozási fáradásteszt), de az agresszív kerékpározás (például a járdaszegély leküzdése) egy teljesen megrakott teherbírású kerékpáron természetesen próbára teszi bármely váz határait. Durva városi használatra tervezzük a vázainkat – például a vázaink valamivel több anyaggal rendelkeznek a láncvillák kereszttartóján, hogy ellenálljanak a pedálnyomatékoknak és az alkalmi rázkódásoknak –, de azt is felvilágosítjuk a kerékpárosokról, hogy a sima kerékpározás hosszú élettartammal jár. Hasonló egy teherautóhoz: normál paraméterek között vezesd, és sok évig kitart; folyamatosan tedd ki terepjárásnak, és még a legkeményebb teherautónak is több karbantartásra lesz szüksége végül.
Környezeti és használati tényezők: A valós körülmények között a tartósságot a környezet is befolyásolja. Az esős, tengerparti városokban használt kerékpárok korróziónak vannak kitéve (amit bevonatokkal kezeltünk). A kézbesítő szolgáltatások által használt kerékpárok egész nap kint lehetnek a napon, ezért UV-stabil bevonatokat alkalmazunk a festék degradációjának megakadályozására. A hőmérséklet-ingadozások az anyagok tágulását/összehúzódását okozhatják – ez általában nem probléma a fémvázaknál, de a műanyag alkatrészek esetében figyelembe kell venni. Tervezési alapelvünk, hogy figyelembe vesszük a következőket: legrosszabb forgatókönyv ...egy átlagos felhasználó találkozhat vele, és megbizonyosodhatunk arról, hogy a váz elbírja. Például azt kérdezzük: mi van, ha a kerékpárt kicsit túlterheljük, majd hidegben áthajtunk egy járdaszegélyen? Ez a forgatókönyv több stresszort rétegez. Összetett forgatókönyvek (túlterhelés + ütés laboratóriumi teszteken) tesztelésével célunk biztosítani, hogy még ez se okozzon katasztrofális meghibásodást. Lehet, hogy túllépi az ajánlott használatot (és ezt biztosan nem javasoljuk), de a rugalmasság bizonyos mértékű kiépítése a tartósság mérnöki tudományának része.
Karbantartás és ellenőrzések: Egy tartós váznak a rendszeres ellenőrzés is előnyére válik. Használat közben olyan dolgok, mint a csavarok meglazulása, másodlagos problémákat okozhatnak (pl. egy laza csavar zörgése károsíthatja a vázrögzítést). Ezért a mi... Szolgáltató központ A dokumentáció és a dokumentáció hangsúlyozzák a váz és a rögzítési pontok rendszeres ellenőrzését. Útmutatást adunk a festéklepattogzások vagy rozsdafoltok ellenőrzéséhez és kijavításához, a hegesztési területek repedések vagy festékfeszültségek jeleinek vizsgálatához (bár rendkívül ritka, hogy ilyet találjunk, ha a fenti lépéseket jól végezzük). A motoros vagy a flottaszerelő szerepet játszik a problémák korai jeleinek felismerésében. Vázainkat alacsony karbantartási igényűre tervezzük (nincs semmilyen „vázkarbantartás” a tisztán tartáson és a kijavításon kívül), de proaktív hozzáállást támogatunk: ha valamit észreveszel, foglalkozz vele, mielőtt az megnőne. A jó tervezés és a felelősségteljes használat közötti partnerség biztosítja, hogy a váz valóban elérje a tervezett élettartamát.
Valós pályaeredmény: Egy dolog elméletben beszélni, de egy másik látni, hogy a vázak évek után is erősek. Az Regen viszonylag fiatal, de csapatunk évtizedes tapasztalattal rendelkezik az iparágban. Láttuk már OEM vázainkat nehéz körülmények között használni – a gyerekeket naponta szállító családi kerékpároktól kezdve a hajnaltól alkonyatig csomagokat szállító logisztikai e-bike-okig. A visszajelzések nagyon pozitívak voltak: vázaink megtartják az illeszkedésüket, nincs repedés- vagy problémajárvány, és az ügyfelek megjegyzik a masszív érzetet még hosszas használat után is. Büszkék vagyunk erre, de soha nem pihenünk – minden vázfrissítés lehetőséget ad a tartósság további javítására, gyakran a terepi adatokból gyűjtött apróbb fejlesztések beépítésével.
Végső soron egy teherkerékpár váza kemény életet él a világban. Azzal, hogy megértjük ezeket a valós erőket és viselkedéseket, és ennek megfelelően tervezzük/teszteljük, biztosítjuk, hogy vázaink – és tágabb értelemben az Ön kerékpárjai – évről évre bírják a mindennapi munkát. Minden a következőről szól: szerkezeti állóképesség: nemcsak egyetlen próbát él túl, hanem számtalan szállításon, családi túrán vagy kalandon keresztül is helytáll. Ez a tartósság igazi védjegye.
Következtetés
Egy teherbicikli vázának tartóssága több tényező szinergiájából fakad. A következővel kezdődik: intelligens anyagválasztás (a megfelelő fém felhasználásával és megfelelő kezelésével) befolyik átgondolt geometria és robusztus illesztési kialakítás (így a terhelések jól eloszlanak), a következők biztosítják: kiváló minőségű hegesztés és precíziós gyártás (a gyenge láncszemek kiküszöbölésével), és ezt bizonyítja a szigorú tesztelés és valós körülmények között történő validálás (így egyetlen feltételezés sem marad ellenőrizetlen). Rétegek hozzáadása korrózióvédelem megőrzi ezt az erőt hosszú távra, és a megértés valós használat irányítja mind a tervezésünket, mind a felhasználók oktatását, hogy ezek a keretek erősen gördüljenek.
Az Regen-nél, ahol nap mint nap teherkerékpár-vázakat tervezünk, építünk és szerelünk össze, első személyű nézőpontunkból hangsúlyozzuk, hogy a tartósság nem a véletlen műve – hanem mérnöki munka eredménye. Minden döntésünk, a 6061-T6 alumínium kiválasztásától és ED bevonatolásától kezdve a fejcső megerősítésén át az egyes villapapucsok milliméteres pontosságú beállításáig, hozzájárul ahhoz, hogy olyan vázat kapjunk, amelyben a megélhetésünket (vagy családunk biztonságát) tudhatjuk. Teherkerékpár-gyártóként (OEM/ODM) a hírnevünk ugyanúgy ezeken a vázakon múlik, mint ügyfeleinkén. Ezért minden lépésnél befektetünk a tartósságba, és világszerte szakértőkkel működünk együtt (Kínában a hatékony gyártásért, Portugáliában a kiváló minőségű összeszerelésért és minőségellenőrzésért), hogy mindkét világból a legjobbat nyújtsuk.
Gyakorlatilag mit jelent ez számodra, olvasó számára? Ha teherbicikli-márkád van, az azt jelenti, hogy magabiztosan testre szabhatod a következő modelledet, tudván, hogy az alatta lévő platform kőkemény – és mi itt vagyunk, hogy megoldási partnerként segítsünk. Ha kerékpáros vagy flottaüzemeltető vagy, ez nyugalmat jelent: egy jól megépített teherbicikli-váz. lehet, hogy ez a legkisebb gondod még akkor is, ha a határait feszegeted. És ha csak kíváncsi vagy, reméljük, hogy értékelni kezded azt a mérnöki igényességet, amelyet ebbe a szerénynek tűnő csőszerkezetbe fektetnek, amelyben az élelmiszereket vagy csomagokat szállítod.
A váz szilárdsága és tartóssága nem varázslat – a tudás, az erőfeszítés és a minőség eredményei. Az Regen-nél szenvedéllyel beszélünk ezekről a témákról, mert szó szerint a mi dolgunk olyan kerékpárokat készíteni, amelyek tartósak. Reméljük, hogy ez a mélyreható elemzés eloszlatta a téma rejtélyeit, és megmutatta, hogy miért hoznak bizonyos döntéseket az iparágban. Egy teherkerékpár vázának sokat kell kitartania, de a megfelelő megközelítéssel ezt kecsesen és megbízhatóan megteheti. Itt a lendület az idő (és a nehéz terhelés) próbáját kitartó kerékpárok építéséhez!
Referenciák
- Hambini Mérnöki Iroda. (2023). Kerékpárváz gyártási szabványok. (Betekintés az OEM vázgyártásba és a minőségbiztosítás/minőség-ellenőrzés fontosságába a megbízhatóság biztosításában)
- Serfas. (második). Kerékpárváz anyagok: Ismerd meg a különbségeket. (Az alumínium, acél, titán és karbon jellemzőinek áttekintése; megjegyzi, hogy az alumínium vázak gyorsabban fáradnak ki, míg az acél nagyon ellenálló a fáradási folyamattal szemben)
- Singh, G. (é.n.). 1000 órás sópermet-állóság a vasalaton – Finishing.com fórum. (Az iparági szakértők véleménye szerint a katódos elektrobevonat megfelel az ASTM B117 sópermet-állóságnak több mint 1000 órán át, vörös rozsda nélkül)
- Tern Bicycles. (második). Hogyan teszteljük teher- és személyszállító kerékpárjaink biztonságát?. (A Tern teherkerékpár-vázak vizsgálati protokollja, beleértve a belső „hibateszt” módszereket és a DIN 79010 szabványok túllépését)
- Vello Bikes. (2023. október 23.). A VELLO SUB új mércét állít fel az EFBE-TRI-TEST® teszttel. (Bejelentés arról, hogy a teherkerékpár megfelelt az EFBE Tri-Test vizsgán; ismerteti a Tri-Test 100 000 ciklusos fáradási és túlterhelési próbáit a vázakra vonatkozóan)