Como proveedor de soluciones OEM/ODM para bicicletas de carga, Nosotros en Regen Sepa que el cuadro de una bicicleta es su columna vertebral. La resistencia del cuadro no se trata solo de sostener la bicicleta; se trata de transportar con seguridad carga valiosa, sobrevivir años de uso diario e inspirar confianza al ciclista. En este artículo, exploraremos desde una perspectiva directa qué determina realmente la durabilidad del cuadro de una bicicleta de carga. Profundizaremos en la ciencia de los materiales, la geometría, la integridad de las soldaduras, los métodos de prueba, la protección contra la corrosión, la precisión de fabricación y la dinámica de carga en el mundo real, todo desde la perspectiva de las bicicletas de carga. A lo largo del camino, compartiremos algunas ideas de nuestra propia experiencia (incluyendo nuestro ensamblaje en Portugal y la fabricación de cuadros en China) y le recomendaremos recursos adicionales para un análisis más profundo. Tanto si es un profesional de la industria de la bicicleta como un entusiasta, esperamos que esta guía le brinde una comprensión clara, cercana y completa de lo que hace que un cuadro de bicicleta de carga sea duradero.
(¿Es nuevo en bicicletas de carga? Consulte nuestra completa Bicicleta de carga 101 (Guía para una introducción a términos y conceptos clave).
Ciencia de los materiales: la base de la resistencia del marco
La elección del material es uno de los factores más fundamentales en la durabilidad del cuadro. Los diferentes materiales de los cuadros, desde aluminio y acero hasta fibra de carbono y otros materiales, tienen propiedades únicas que influyen en la resistencia, la resistencia a la fatiga y la longevidad. Para las bicicletas de carga, que transportan cargas más pesadas que las bicicletas estándar, elegir el material adecuado es fundamental.
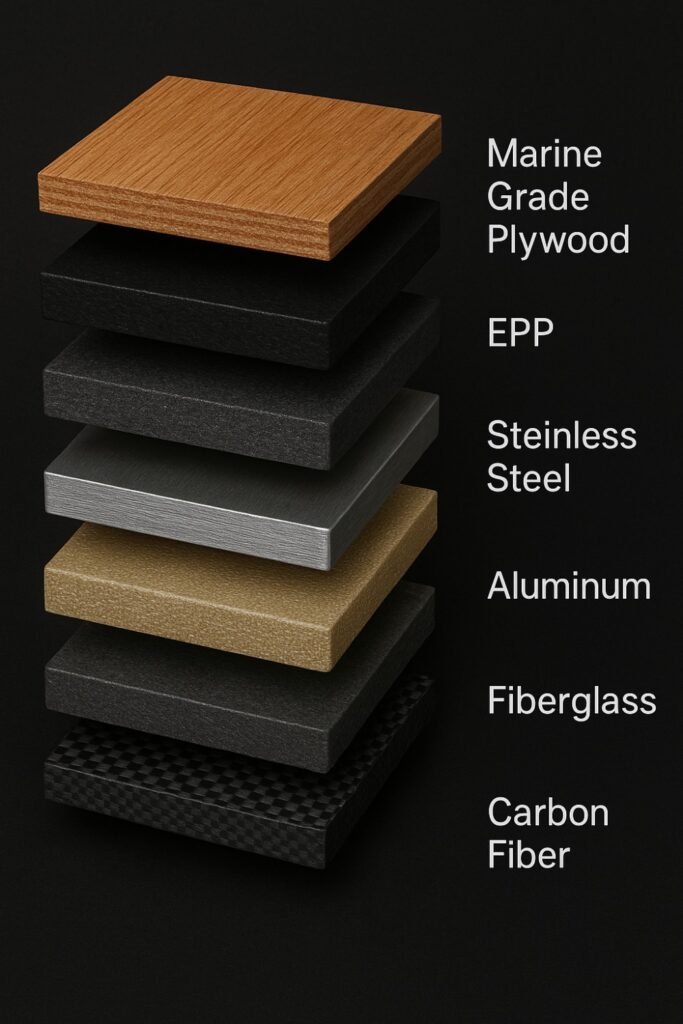
- Aleaciones de aluminio: El aluminio es muy popular en las bicicletas de carga modernas (incluidos nuestros propios cuadros) debido a su ligereza y buena relación rigidez-peso. Las aleaciones de aluminio de alta calidad, como el 6061-T6, proporcionan una estructura resistente y rígida sin el volumen del acero. Sin embargo, el aluminio tiene una desventaja clave: es menos tolerante a los ciclos de tensión repetidos y puede... fatigarse más rápidamente que el acero. En la práctica, un cuadro de aluminio puede tener una vida útil más corta con un uso intensivo, desarrollando microfisuras o fallas antes si no se diseña adecuadamente. Esto no significa que los cuadros de aluminio sean endebles, ni mucho menos. Con un diseño y tratamiento térmico adecuados (el proceso T6 realinea la estructura del grano del metal después de la soldadura), los cuadros de aluminio pueden soportar cientos de kilogramos (nuestros propios... Bicicleta de carga RS01 El bastidor está fabricado en aleación 6061-T6 y soporta una carga útil de hasta 250 kg. Esto implica que los ingenieros deben tener en cuenta la fatiga mediante el uso de tubos de paredes más gruesas o refuerzos adicionales en zonas de alta tensión. (¿Tiene curiosidad por saber cómo se compara el aluminio con otros metales? Consulte nuestra Comparación de materiales de marco: aluminio, acero y otros (para una mirada en profundidad.)
- Acero (de alta resistencia y cromoly): El acero es el material clásico para los cuadros de bicicletas y sigue siendo un caballo de batalla para la durabilidadUn cuadro de acero bien fabricado puede durar décadas. Su dureza y elasticidad inherentes le otorgan una excelente resistencia a la fatiga del metal. Puede absorber impactos y vibraciones (como baches o desniveles) sin agrietarse, por lo que muchas bicicletas de carga resistentes o cuadros de cola larga diseñados para una máxima durabilidad utilizan acero. Además, si un cuadro de acero se agrieta, a menudo se puede reparar con soldadura, lo que mejora su durabilidad. Las desventajas: el acero es más pesado, lo que dificulta pedalear o levantar la bicicleta, y propenso a la corrosión (óxido) si no se protege. En las bicicletas de carga, el peso es menos importante que en las de carreras, por lo que la compensación por la durabilidad suele merecer la pena. Muchas bakfiets (bicicletas de caja) y bicicletas de montaña utilizan aleaciones de acero al cromo-molibdeno para aprovechar esa resistencia y resiliencia. En Regen, a veces elegimos acero de alta resistencia para... bicicletas de carga industriales Donde la máxima resistencia y una conducción suave son la máxima prioridad. (La indulgencia del acero puede ser una ventaja al transportar carga o pasajeros frágiles). Una adecuada prevención de la oxidación (que abordaremos más adelante) es esencial para mantener la resistencia de un chasis de acero resistente.
- Fibra de carbono: Los cuadros de polímero reforzado con fibra de carbono son famosos por ser ligero y rígidoCon una excelente relación resistencia-peso. Sin embargo, el carbono es poco común en las bicicletas de carga, y con razón. Los cuadros de carbono carecen de ductilidad De metal: no se doblan ni se deforman antes de romperse, simplemente se fracturan al ser sometidas a una tensión excesiva. Bajo las cargas pesadas y cambiantes que soportan las bicicletas de carga, un cuadro de carbono podría ser vulnerable a fallos repentinos si se daña. El carbono también tiene baja resistencia al impacto (un golpe fuerte puede provocar una grieta). Para una bicicleta de carreras, reducir el peso es primordial, pero para una bicicleta de carga, la durabilidad y la fiabilidad a largo plazo son aún más importantes. El coste del carbono y la dificultad de reparación limitan aún más su uso en este ámbito. En resumen, si bien una bicicleta de carga de carbono no es imposible, no suele ser la opción óptima en cuanto a durabilidad. (Para una discusión experta sobre cuadros de carbono frente a cuadros de metal, consulte Radar de bicicletas(Guía de materiales para marcos).
- Titanio y otros: El titanio a veces se denomina el "material ideal": tan resistente como el acero, pero más ligero y absolutamente inoxidable. Existen bicicletas de carga de titanio, pero son extremadamente poco comunes debido a su... Fabricación muy costosa y especializadaEs difícil de soldar y trabajar, lo que implica una producción costosa. Para proyectos a medida o marcas de alta gama, los cuadros de titanio pueden ofrecer una durabilidad excepcional (prácticamente no se corroen y tienen una resistencia a la fatiga similar a la del acero). Sin embargo, la mayoría de las marcas de bicicletas de carga (y operadores de flotas) no buscan el precio que exige el titanio. Otros materiales especializados incluyen laminados de madera o bambú (con refuerzo compuesto), que se han utilizado en algunas bicicletas para amortiguar las vibraciones; son interesantes, pero no son comunes en aplicaciones de carga.
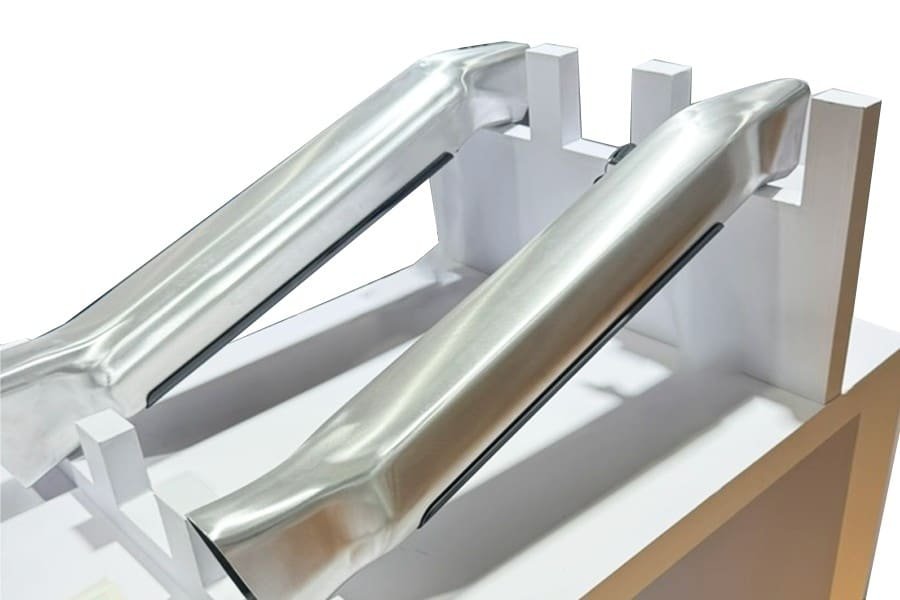
En resumen: Hoy en día, el aluminio y el acero dominan la construcción de cuadros de bicicletas de carga para equilibrar la resistencia, el peso y el costo. . El aluminio ofrece ahorro de peso y es muy rígido, pero debe diseñarse para mitigar la fatiga. El acero ofrece una durabilidad y una conformidad inigualables a largo plazo, a costa del peso adicional y la protección contra la oxidación necesaria. La elección del material define el marco para todas las demás consideraciones de diseño para lograr un cuadro duradero.
(Lectura relacionada: nuestro artículo anterior sobre Factores clave que afectan la capacidad de carga de las bicicletas de carga (Aborda cómo el material y la construcción del cuadro influyen en el peso que puede soportar una bicicleta).
Geometría del cuadro: la forma es importante para la durabilidad
Más allá de lo que está hecho un marco, Cómo se forma y estructura el marco Influye enormemente en su resistencia y vida útil. La geometría no se limita solo al manejo y la sensación de conducción (aunque eso también es importante; consulta nuestra publicación sobre... Cómo afecta la geometría del cuadro al manejo para esa perspectiva); también determina cómo se distribuyen las tensiones a través del marco.
Un cuadro de bicicleta es esencialmente una estructura diseñada. Los triángulos son tus amigos: El cuadro clásico de bicicleta de diamante utiliza dos triángulos entrelazados porque esta forma no se deforma fácilmente. Sin embargo, las bicicletas de carga a menudo se desvían de la forma de diamante: pueden ser bicicletas alargadas de cola larga o de carga frontal. Calzoncillos largos Con una caja de carga, o incluso triciclos. Estos diseños introducen nuevas consideraciones geométricas para mantener la resistencia:
- Reforzando áreas críticas: Los cuadros de bicicletas de carga suelen incluir tubos o refuerzos adicionales para reforzar las uniones sometidas a altas tensiones. Por ejemplo, una bicicleta de carga frontal (Long John) suele tener un tubo largo y extendido que conecta la rueda delantera al cuadro principal. Esta zona puede estar triangulada con puntales adicionales para evitar la flexión. Asimismo, el tubo de dirección (donde se conecta la horquilla) está sometido a grandes fuerzas, especialmente bajo cargas pesadas y frenadas. Es habitual añadir refuerzos o travesaños cerca de la unión del tubo de dirección y el tubo superior/inferior para distribuir la tensión y evitar grietas. Estos elementos de diseño garantizan que ningún tubo soporte toda la carga por sí solo. En términos de ingeniería, nuestro objetivo es reducir la concentración de tensiones; estas pueden ser puntos de inicio de fallos si no se abordan.
- Ruta de carga y distribución del peso: La geometría de las bicicletas de carga a menudo está diseñada para transportar cargas de forma segura. centro de gravedad bajo Es deseable para la estabilidad, por lo que las bicicletas con caja delantera ubican la carga entre las ruedas. Una bicicleta con caja trasera larga extiende el triángulo trasero para acomodar el peso de la carga o del pasajero sobre la rueda trasera. En ambos casos, el cuadro debe tener una forma que mantenga el peso equilibrado y la estabilidad. sin Presentando puntos débiles. Las secciones horizontales largas (como una plataforma de carga o tirantes traseros extendidos) pueden apoyarse en tirantes diagonales. En Regen, utilizamos análisis de elementos finitos (FEA) durante el diseño para simular cómo las diferentes formas de cuadro soportan las cargas, ajustando la geometría para lograr un equilibrio óptimo entre resistencia y peso. Por ejemplo, el cuadro del área de carga de nuestra RS01 es un enrejado cuidadosamente diseñado que soporta hasta 250 kg sin flexión excesiva, manteniendo el centro de masas de la moto bajo.
- Diseños específicos de bicicletas de carga: Cada tipo de geometría de bicicleta de carga tiene sus ventajas y desventajas en cuanto a durabilidad. John largo (bicicleta con caja delantera) a menudo tiene una dirección robusta y un cuadro extendido: más juntas y piezas, pero también una distribución de carga generalmente bien equilibrada. Cola larga Parece más una bicicleta normal, pero estirada; puede concentrar mucho peso sobre la rueda trasera y los tirantes superiores, lo que requiere soldaduras fuertes y posiblemente tubos más gruesos en esa zona. triciclo de carga de tres ruedas Tiene una base ancha y estable, pero su cuadro puede experimentar torsión al girar si una rueda se levanta o en terreno irregular. Por ello, los cuadros de triciclo a veces incorporan travesaños adicionales para reforzarlos y evitar la torsión. Cada geometría (trasera, eje de bicicleta, etc.) requiere un diseño estructural meticuloso para evitar flexiones o fallos bajo carga.
Para ilustrarlo, consideremos el Retirada del mercado de bicicletas de carga Babboe Que fue noticia en la industria: los problemas con el cuadro se atribuyeron en parte a decisiones de diseño que no manejaron adecuadamente las tensiones del mundo real. Algunos cuadros se agrietaron en el tubo inferior debido a una combinación de problemas de diseño y soldadura. Esto demuestra que incluso con un material resistente, Una geometría estructural deficiente o un refuerzo insuficiente pueden provocar problemas de durabilidad. Tomamos esas lecciones en serio en nuestros propios diseños.
En resumen, un cuadro de bicicleta de carga duradero es Diseñado para la fuerzaEl uso estratégico de triángulos, arcos y tirantes fortalece la estructura. La geometría debe ser acorde con el uso previsto: un cuadro diseñado para cargas pesadas podría incluir un tubo superior arqueado para facilitar el paso, pero reforzado con un tubo inferior adicional para mayor resistencia, por ejemplo. El diseño de cuadros implica arte y ciencia: arte en crear una forma práctica, ciencia en garantizar que la forma resista el paso del tiempo. (Para más información sobre los distintos diseños de cuadros de bicicletas de carga y sus características, consulte nuestra explicación en Diferentes tipos de cuadros de bicicletas de carga en el Glosario de bicicletas de carga serie.)
Soldaduras e integridad de las juntas: creando una conexión sólida
Incluso los mejores materiales y geometrías pueden verse socavados por una cosa: soldaduras o uniones débiles. Los puntos donde se unen los tubos (soldados o soldados con soldadura fuerte) son típicamente los zonas de mayor estrés En un cuadro. No es de extrañar que muchas fallas en el cuadro se originen en las soldaduras o alrededor de la zona afectada por el calor junto a una soldadura. Para una bicicleta de carga que transporta cargas pesadas, garantizar la integridad de la soldadura es fundamental.
En Regen, solemos decir que la resistencia del chasis depende de su soldadura más débil. ¿Qué hace que una unión sea resistente?
- Técnicas de soldadura de calidad: La mayoría de los cuadros metálicos de bicicletas de carga utilizan soldadura TIG (gas inerte de tungsteno) o MIG para fusionar los tubos. La soldadura TIG, realizada por personal experto o un sistema robótico de precisión, permite un control preciso para crear cordones resistentes y consistentes. El objetivo es la penetración completa de la soldadura (es decir, que el metal de soldadura se fusione completamente a través de la unión con el metal base) sin defectos. En la producción de cuadros de aluminio, es habitual tratar térmicamente todo el cuadro después de la soldadura (devolviéndole el temple T6), ya que el calor de la soldadura puede ablandar el aluminio en esa zona. Omitir este paso puede debilitar la zona de soldadura. En marcos de aceroTécnicas como la soldadura fuerte (con terminales) o la soldadura TIG pueden funcionar. Las uniones soldadas TIG pueden reforzarse con pequeños refuerzos si es necesario. Es fundamental que el metal de soldadura no presente grietas, huecos ni inclusiones.
- Inspección y Prueba de Soldaduras: En nuestras fábricas, las soldaduras de cada cuadro se inspeccionan visualmente y, a menudo, probado de forma no destructivaLas pruebas con líquidos penetrantes, por ejemplo, pueden revelar microfisuras en una soldadura: el técnico aplica un tinte y revelador especiales para resaltar cualquier defecto demasiado pequeño para ser visible a simple vista. Los fabricantes de cuadros de alta gama (especialmente para cuadros de bicicletas eléctricas de alta gama) pueden incluso realizar inspecciones por rayos X o ultrasonidos en las soldaduras, de forma similar a los estándares aeroespaciales. Este nivel de control de calidad garantiza que no se filtren defectos ocultos. Es este tipo de diligencia la que evita que una pequeña fisura se convierta en un fallo grave en el futuro.
- Diseño de la articulación: Algunas articulaciones son inherentemente más robustas que otras. Por ejemplo, juntas de doble cizallamiento (donde un tubo se superpone entre dos placas o tacos) puede ser más resistente que una unión a tope. En las bicicletas de carga, es frecuente ver manguitos o collarines de refuerzo alrededor de uniones sometidas a alta tensión, como el tubo de dirección o el conjunto del tubo del sillín. Estos manguitos distribuyen la carga y reducen la tensión en la propia soldadura. Otra técnica es conformación de boca de pez de los extremos del tubo: el tubo está contorneado para encajar a ras con el tubo de acoplamiento para la soldadura, maximizando así el área de contacto. Incorporamos estos detalles en nuestros diseños de bastidor para garantizar que las soldaduras no sufran sobrecargas. Además, utilizando cordones de soldadura suaves y continuos (en lugar de la soldadura intermitente) puede ayudar a eliminar los acumuladores de tensión. Una soldadura bien ejecutada debe tener la apariencia de una pila ordenada de monedas, envolviendo uniformemente la unión.
¿Por qué importa todo esto? Consideremos el desafortunado caso mencionado anteriormente: una importante marca tuvo que retirar bicicletas del mercado debido a... “Soldadura inadecuada y fallas de diseño” que provocan fallas del bastidor bajo presión . En ese caso, es probable que algunas soldaduras presentaran defectos o que el diseño de la unión fuera insuficiente, lo que provocaba grietas al cargar la moto. La lección es clara: una soldadura deficiente no es una opción cuando la seguridad está en juego. Por eso, los socios de fabricación de Regen en China siguen estrictos procedimientos de soldadura (conformes a las normas ISO y EN) y nuestra planta de ensamblaje en Portugal realiza controles de calidad finales en cada lote.
En breve, Soldaduras fuertes y limpias = cuadros duraderosEs un trabajo minucioso que requiere habilidad, el equipo adecuado y un control de calidad impecable. Pero esa inversión se amortiza al eliminar prácticamente uno de los puntos de fallo más comunes en los cuadros de bicicleta. La próxima vez que vea una bicicleta de carga, revise los cordones de soldadura: pueden revelar mucho sobre la calidad de construcción del cuadro.
Pruebas de fatiga y estrés: Validación de la fuerza a lo largo del tiempo
Diseñar y construir un cuadro resistente es una cosa; prueba Su durabilidad es otro factor. Aquí es donde entran en juego las rigurosas pruebas de fatiga y estrés. Sometemos nuestros cuadros a pruebas simuladas de laboratorio y en condiciones reales para garantizar que resistan las tensiones repetitivas y los impactos ocasionales del ciclismo de carga durante muchos años. Analicemos cómo funcionan las pruebas de cuadros y por qué son vitales.
Pruebas de fatiga de laboratorio: En las pruebas de laboratorio, se monta un cuadro en soportes y se somete a fuerzas controladas que simulan el pedaleo, el frenado y los baches, repetidas miles y miles de veces. Por ejemplo, una prueba común es... prueba de fatiga del pedal El cuadro se sujeta en las punteras traseras y se aplica una carga cíclica donde estaría el pedalier/cadena, imitando las fuerzas de un ciclista que pedalea con fuerza. Otra es la prueba de fatiga del tubo de dirección, donde las fuerzas tuercen la horquilla/parte delantera como si chocara contra baches o el ciclista forcejeara con el manillar. Estándares de la industria como ISO 4210-6 (para cuadros de bicicletas) y los nuevos específicos para carga DIN 79010 (2020) Especificar este tipo de pruebas con cargas definidas y recuentos de ciclos. Para aprobar, un cuadro podría necesitar sobrevivir, por ejemplo, 100.000 ciclos de carga sin desarrollar grietas.
Los estándares para bicicletas de carga elevan aún más el estándar. La norma alemana DIN 79010 y la futura norma europea EN 17860 reconocen que las bicicletas de carga se someten a... tensiones más altas que las bicicletas normales. Por lo tanto, las cargas de prueba son más pesadas y se incluyen pruebas adicionales (como la capacidad de transporte de pasajeros). Muchos fabricantes (incluidos nosotros) buscan la certificación independiente de estos estándares. Por ejemplo, colaboramos con laboratorios de pruebas para realizar la batería completa de pruebas en nuestros cuadros. En algunos casos, incluso superamos el estándar: los cuadros se someten a pruebas hasta que... fallar para ver cuánto maltrato pueden soportar. Este enfoque de "prueba de destrucción" ayuda a identificar el eslabón más débil y nos da un margen de seguridad más allá del uso normal. (Un fabricante de bicicletas de carga, Tern, señaló que algunos de sus cuadros eran tan robustos que las máquinas de laboratorio tuvieron que detenerse porque el cuadro... no lo haría break – un testimonio de ingeniería exhaustiva.)
Un gran ejemplo de prueba de cuadro extrema es el Prueba Tri-Test® de EFBE Protocolo desarrollado en Alemania. Se trata de una prueba de tortura específica para cuadros de bicicletas de carga que va mucho más allá de los estándares básicos. En la Tri-Test, un cuadro y una horquilla se someten a una serie de pruebas de fatiga, carga máxima e incluso sobrecarga en múltiples direcciones. Los cuadros pueden ser sometidos a cientos de miles de ciclos de tensión desde diferentes ángulos, simulando una vida útil completa en formato condensado. De hecho, como parte de la Tri-Test, los cuadros resisten aproximadamente... 100.000 ciclos repetitivos Bajo carga pesada, junto con pruebas de impacto independientes. Superar esta prueba le otorga al cuadro la certificación de que está a la altura del transporte de carga en condiciones reales. Nos inspiramos en estos rigurosos protocolos al probar nuestros propios diseños (aunque no todos los cuadros pasan la prueba oficial EFBE, la filosofía es la misma: llevarlo al límite y más allá).
Pruebas de carga estática e impacto: Además de los ciclos de fatiga repetidos, las pruebas de durabilidad también incluyen pruebas de carga estática (aplicación gradual de una carga pesada para ver si el cuadro cede o se deforma) y pruebas de impacto (dejar caer un peso sobre el cuadro o golpearlo en puntos específicos para simular un choque o un impacto contra la acera). Un ejemplo es el prueba de caída del marcoSe deja caer una masa pesada sobre un marco o se deja caer el marco desde cierta altura para comprobar que no se agriete. Otra es la prueba de sobrecarga: colocar significativamente más peso que la capacidad nominal en el área de carga para garantizar un margen de seguridad. Estas pruebas verifican no solo la rotura inmediata, sino también cualquier... deformación permanente Un cuadro resistente debe recuperarse y mantenerse alineado si el impacto se produce dentro de los escenarios previstos. Normas como la EN 17860 detallan estas pruebas para que los cuadros cumplan con los requisitos de seguridad antes de su llegada al consumidor.
Pruebas en el mundo real: Las pruebas de laboratorio son esenciales, pero también creemos en las tradicionales pruebas en carretera. Antes de finalizar el diseño de un cuadro, construimos prototipos de bicicletas y... Úsalos con fuerza en condiciones reales Adoquines, baches, carga completa, cuestas empinadas, frenadas repentinas... lo que sea. Estas pruebas experimentales a menudo revelan problemas que un laboratorio podría no detectar (o validan que las simulaciones de laboratorio fueron precisas). Por ejemplo, un cuadro puede superar las pruebas de fatiga de laboratorio con éxito, pero al ser utilizado por diversos ciclistas, podríamos descubrir una flexión inesperada en el área de carga o un ligero aflojamiento en una junta después de un mes de uso similar al de un mensajero. Este ciclo de retroalimentación nos permite refinar los procesos de soldadura o añadir refuerzos antes de la producción en masa. Muchos fabricantes líderes realizan pruebas piloto similares, animando al personal o a los probadores beta a alcanzar un kilometraje considerable en los nuevos modelos. No es raro ver a nuestros ingenieros cargando una bicicleta de carga con sacos de arena y subiendo y bajando repetidamente una colina de prueba cerca de nuestras instalaciones, intentando someter a prueba los frenos y el cuadro. El lema aquí es... “validar, validar, validar.”
Cuando un cuadro supera todas estas pruebas, tanto de laboratorio como de campo, podemos afirmar con seguridad que es duradero. Además, lo respaldamos con sólidas garantías. (Regen ofrece una garantía de cuadro de varios años y un sólido servicio posventa a través de nuestro... Centro de servicio Porque hemos probado nuestros productos para garantizar su durabilidad. Si surge algún problema durante el uso del cliente, lo analizamos y aplicamos esa información a la siguiente revisión del diseño.
Y como siempre, no dude en comunicarse con nosotros en Regen si tiene preguntas específicas o necesita un socio ODM que viva y respire la durabilidad de las bicicletas de carga.
En resumen, Las pruebas de fatiga y estrés son donde la ingeniería se encuentra con la realidad.Es un paso crucial para garantizar que la resistencia teórica se mantenga durante innumerables viajes. Si estás evaluando proveedores de bicicletas de carga, es recomendable preguntar: ¿Cumplen las pruebas con los estándares pertinentes? ¿Superan los requisitos mínimos? Un cuadro duradero no nace de la nada; es... probado a través de exámenes tan rigurosos, brindando a los conductores y operadores de flotas la tranquilidad de que estas motos no flaquearán cuando las cosas se pongan difíciles.
Protección contra la corrosión: combatiendo los elementos para una mayor longevidad
Imagine dos cuadros de bicicleta de carga de acero idénticos: uno empieza a oxidarse en un año y acaba debilitándose en las juntas críticas; el otro resiste la lluvia y la sal de la carretera, luciendo y funcionando como nuevo incluso después de años. ¿La diferencia? Protección contra la corrosión. Un factor fundamental en la durabilidad del cuadro es su protección contra los elementos: el agua, la sal e incluso la exposición a los rayos UV pueden degradar los materiales con el tiempo. Esto es especialmente importante para los cuadros de acero (que pueden oxidarse), pero también para el aluminio (que puede corroerse, aunque de forma diferente) y para la durabilidad de la pintura y las calcomanías.
En Regen, damos la misma importancia a la protección contra la corrosión que al diseño estructural. Nuestro enfoque suele implicar un proceso de recubrimiento multicapa, siendo la pieza clave el... Recubrimiento ED (recubrimiento por deposición electroforética)También conocido como recubrimiento electrolítico. Esto es lo que hacemos y por qué es importante:
- Imprimación de recubrimiento ED: El recubrimiento ED es una técnica de pintura avanzada, propia de la industria automotriz. En resumen, el chasis se sumerge en un baño de pintura especial con carga eléctrica, lo que crea un recubrimiento uniforme y de gran adherencia sobre todas las superficies, tanto por dentro como por fuera. Es como una imprimación antioxidante que llega incluso a los rincones más ocultos del chasis: paredes internas de los tubos, grietas de soldadura, etc., donde la pintura en aerosol o el recubrimiento en polvo podrían no cubrir completamente. Esto es crucial porque El óxido a menudo comienza en lugares invisibles (como dentro de un tubo o debajo de un soporte) y luego se desliza hacia afuera. Con el recubrimiento ED, esas superficies interiores reciben una protección. El resultado es un marco que puede soportar condiciones extremadamente duras. De hecho, los recubrimientos ED catódicos (el tipo que usamos) son conocidos por pasar fácilmente. Más de 1000 horas de pruebas de niebla salina Sin signos de corrosión: un nivel de rendimiento de calidad automotriz. Para ponerlo en perspectiva, 1000 horas en una cámara de niebla salina suponen un uso mucho mayor del que una bicicleta soportaría en años de conducción costera o invernal. Es un buen indicador de "¿se oxidará este cuadro?", y con el recubrimiento ED, la respuesta es no.
- Recubrimiento en polvo y pintura: Sobre la base ED, normalmente añadimos un imprimador duradero. recubrimiento en polvo Para dar color y mayor espesor. El recubrimiento en polvo consiste en aplicar electrostáticamente un polvo seco y hornearlo, formando una capa resistente de pintura. Resiste el descascarillado y los rayones mejor que la pintura húmeda tradicional. Esta es la capa de color principal. Finalmente,... capa transparente Se puede aplicar laca o barniz para obtener protección UV y brillo. Cada una de estas capas aumenta la resistencia a la corrosión: si la capa superior se descascara, la capa ED subyacente mantiene a raya la oxidación en un cuadro de acero (y el aluminio, aunque no se oxida, puede oxidarse y debilitar las juntas si no se protege, por lo que el recubrimiento también previene esa oxidación). Nuestras instalaciones en Portugal cuentan con instalaciones de pintura de última generación (una de las razones por las que ensamblamos y acabamos cuadros en la UE es para mantener una estricta calidad en estos pasos de acabado). También ofrecemos acabados personalizados; por ejemplo, los clientes pueden elegir colores RAL personalizados o incluso galvanización para bicicletas de uso especial, pero nosotros Nunca omitas las capas base anticorrosión.
- Herrajes y drenaje de acero inoxidable: Además de la pintura, otras opciones de diseño protegen contra la corrosión. Utilizamos pernos y herrajes de montaje de acero inoxidable siempre que sea posible para que los accesorios o portaequipajes atornillados al cuadro no se conviertan en focos de oxidación. También diseñamos cuadros con orificios de drenaje o ventilación donde sea necesario: si el agua entra en el tubo del cuadro (por la lluvia o el lavado), se seca en lugar de acumularse. Pequeños detalles como este ayudan a garantizar que la humedad no quede atrapada contra el metal. En los cuadros de aluminio, prestamos atención a... corrosión galvánica (cuando el aluminio entra en contacto con el acero en presencia de electrolito, puede corroerse) – separar metales diferentes con arandelas o revestimientos aislantes para evitar tales reacciones.
¿Por qué tomarse tantas molestias? Porque un cuadro podría estar estructuralmente sobreconstruido y nunca agrietarse por la tensión, y aun así fallar prematuramente porque... oxidado por dentro Un asesino silencioso. Hemos visto casos en la práctica (especialmente con bicicletas de carga baratas dejadas a la intemperie) en los que, tras un par de inviernos, la pintura burbujea alrededor de las soldaduras y empieza a aparecer óxido anaranjado. Esto indica que las capas protectoras del cuadro se han roto y la corrosión se ha instalado. Con el tiempo, el óxido puede corroer una soldadura o debilitar la pared de un tubo, reduciendo significativamente su resistencia. Con una protección anticorrosiva robusta como el recubrimiento ED, esta situación prácticamente se elimina: un cuadro bien recubierto podría, en el peor de los casos, presentar solo un poco de óxido superficial superficial si se raya profundamente, pero no se corroerá internamente de forma estructuralmente significativa.
Además, preservar el acabado del cuadro significa que la bicicleta... se ve mejor por más tiempo, lo cual es importante para la imagen de marca de nuestros clientes (nadie quiere que su flota de reparto parezca un virus). También supone una ventaja en materia de seguridad y mantenimiento: las piezas tienen menos probabilidad de agarrotarse o congelarse debido a la oxidación. Pintura personalizada y Calcomanías/Logotipo Todas las opciones funcionan en el marco de mantener esa envoltura protectora: nos aseguramos de que cualquier diseño personalizado o aplicación de logotipo no comprometa las capas subyacentes.
En suma, Un marco duradero debe resistir no solo cargas físicas sino también ambientales.Mediante procesos anticorrosivos de primera calidad, como el recubrimiento ED y un acabado de calidad, esencialmente blindamos nuestros cuadros contra los elementos. De esta manera, con el paso de los años, el factor limitante de la vida útil de una bicicleta de carga es... cuánto trabajo ha realizado – Sin óxido que se arrastra ni pintura degradada. (Para una visión detallada del recubrimiento ED y sus beneficios, consulte nuestro blog de análisis detallado "Recubrimiento ED: protección para cuadros de bicicletas eléctricas y de carga a largo plazo"donde explicamos la ciencia detrás de esto y por qué es un cambio radical en términos de durabilidad).
Precisión en la fabricación: Tolerancias y control de calidad
Al hablar de durabilidad, a menudo nos centramos en factores generales como los materiales y las pruebas. Sin embargo, son igualmente importantes los siguientes: “Pequeños” detalles de precisión de fabricación y control de calidad. El cuadro de una bicicleta de carga no es solo metal pegado, sino una estructura cuidadosamente alineada donde cada milímetro importa. Pequeñas inconsistencias durante la producción pueden generar tensiones o puntos débiles que se manifiestan mucho más tarde. Por eso, en Regen priorizamos las tolerancias de fabricación estrictas y los exhaustivos controles de calidad durante todo el proceso de construcción.
Alineación y tolerancias: Durante la fabricación de cuadros, es fundamental mantener la alineación correcta de todos los tubos. Si la plantilla del cuadro (el soporte que sujeta los tubos para soldar) está ligeramente desalineada, el cuadro podría quedar desalineado; quizás las punteras traseras no sean perfectamente simétricas o el tubo de dirección esté un grado fuera de las especificaciones. Una desalineación podría permitir el montaje y uso de la bicicleta, pero podría significar que, bajo carga, un lado del cuadro soporte más tensión que el otro. Con el tiempo, este desequilibrio puede provocar grietas por fatiga en el lado sobrecargado. Por lo tanto, establecemos tolerancias estrictas: por ejemplo, la alineación de las punteras con una precisión inferior a 1 mm, el paralelismo entre el tubo de dirección y el tubo del sillín con una precisión de una fracción de grado, y las caras de la caja del pedalier mecanizadas planas y paralelas. Muchos fabricantes de bicicletas de renombre buscan valores similares (del orden de 0,5 a 1 mm de tolerancia en dimensiones críticas). Lograrlo requiere utillajes de precisión, soldadores cualificados (ya que el calor de la soldadura puede deformar la alineación al enfriarse) y, a menudo, post-soldadura. fraguado en frío o mecanizado. Revisamos periódicamente los marcos en una mesa de superficie con galgas de alineación después de la soldadura y el tratamiento térmico. Cualquier marco que no cumpla con las especificaciones se puede ajustar con cuidado o, si se desvía demasiado, se puede rechazar. Este nivel de precisión garantiza que cada marco que enviamos sea estructuralmente recto y preciso, de modo que las fuerzas fluyan a través de él según lo previsto por el diseño.
Cómo evitar los factores que aumentan el estrés: Un "aumento de tensión" es un cambio abrupto en el material o la geometría que concentra la tensión (como una esquina afilada o un rectificado incorrecto). Durante la fabricación, evitamos crear aumentos de tensión involuntarios. Por ejemplo, al soldar piezas pequeñas como soportes o topes de cable, nos aseguramos de que estén colocados de forma que no provoquen una concentración de tensión en los tubos principales. Si un cordón de soldadura termina en la superficie de un tubo, lo afilamos y rectificamos suavemente para integrarlo con el tubo. Si se necesita un orificio (por ejemplo, para el cableado interno o para los pernos de montaje), reforzamos esa zona o utilizamos ojales para que el orificio no se convierta en un punto de inicio de grietas. Estas prácticas forman parte de la experiencia de fabricación que distingue un cuadro duradero de uno promedio. Una anécdota: al principio de nuestra producción, observamos una tendencia a la formación de grietas finas cerca de un soporte de portaequipajes específico en un prototipo tras pruebas extremas. Identificamos que el cordón de soldadura de ese soporte terminaba en un punto que se flexionaba. Nuestra solución fue extender el cordón de soldadura para que terminara en una zona de baja tensión, y también aumentar ligeramente el radio de la base del soporte para distribuir la carga. El resultado: se eliminaron las grietas. Este refinamiento iterativo y la atención a los microdetalles solo son posibles con un riguroso control de calidad.
Puntos de control de calidad: Durante la fabricación, múltiples puntos de control de calidad ayudan a detectar problemas. Ya hemos mencionado la inspección de soldaduras y las comprobaciones de alineación. Además, la verificación del material (para garantizar que la aleación utilizada sea exactamente la especificada, por ejemplo, tubos de aleación 6061 originales y no un sustituto más económico) se realiza mediante certificados de materiales de los proveedores y, en ocasiones, pruebas puntuales. También realizamos inspecciones del acabado superficial: se revisa toda la superficie del cuadro después del recubrimiento para detectar cualquier poro o hueco en la pintura que pueda provocar corrosión posterior. Nuestro equipo de montaje en Portugal realiza una construcción final de cuadros de muestra aleatorios para verificar que todo encaje perfectamente; si un cuadro tiene un saliente mal colocado o una ligera distorsión, se detectará al intentar instalar los componentes. Este exhaustivo proceso de control de calidad forma parte de la fiabilidad de un OEM. Como bien señaló un experto del sector, con un control de calidad y una supervisión adecuados, las variaciones de fabricación se pueden controlar rigurosamente y se puede lograr una alta consistencia, independientemente de la ubicación de producción. En otras palabras, son los sistemas y estándares que se aplican los que determinan la calidad. Colaboramos con nuestra fábrica de cuadros para implementar... Procesos certificados según la norma ISO 9001 Monitoreamos continuamente la producción. El objetivo es que cada cuadro que salga de la línea sea tan bueno como el primer artículo que aprobamos.
Tolerancias de fabricación en la práctica: ¿Qué implica todo esto para la durabilidad? Significa que cada cuadro se construye según lo concebido por el ingeniero. Unas cajas de pedalier correctamente orientadas evitan la tensión en los rodamientos (si un pedalier no está a escuadra, puede generar tensión en la caja o en el eje de la biela). Unas punteras bien alineadas permiten que la rueda trasera se asiente recta, de modo que las cargas izquierda/derecha estén equilibradas. Un tubo de dirección centrado evita que la horquilla se desvíe sutilmente hacia un lado, lo que podría causar tensión asimétrica en el tubo diagonal. Todos estos pequeños factores preservan la integridad del cuadro a lo largo del tiempo. Además, la fabricación de precisión garantiza un manejo predecible de la bicicleta (lo que indirectamente también afecta a la durabilidad: menos bamboleo y flexión significan menos riesgo de cargas extrañas o caídas).
En la fabricación, nos gusta decir “cero defectos” Es el objetivo. Si bien la perfección es un camino, no un destino, al aspirar a ella reducimos drásticamente la posibilidad de que un defecto oculto acorte la vida útil de un cuadro. Por eso invertimos en artesanos cualificados, equipos adecuados y una formación exhaustiva tanto en nuestra planta de cuadros de China como en nuestra planta de montaje de Portugal. Esta última, una fábrica de vanguardia de 49.000 m² en Águeda, Portugal, nos permite realizar el ajuste y el montaje finales en Europa, lo que añade un nivel adicional de control de calidad y garantiza el cumplimiento de las normas de la UE en el continente. Esta combinación de fabricación eficiente y acabado meticuloso es la que nos permite ofrecer cuadros duraderos a gran escala.
(Para echar un vistazo detrás de escena, nuestro Acerca de Regen Esta página detalla nuestro enfoque de fabricación integral, incluyendo cómo nuestra producción de cuadros en China y nuestro ensamblaje en Portugal trabajan en conjunto para lograr una alta calidad. Y si le interesa personalizar las especificaciones o características del cuadro manteniendo tolerancias estrictas, consulte nuestra Configuración funcional personalizada Servicios: podemos adaptar los diseños a sus necesidades sin comprometer nuestros estándares de control de calidad).
Rendimiento en el mundo real: dinámica de carga e influencia del uso
Por último, hablemos del campo de pruebas definitivo para la durabilidad del cuadro: uso en el mundo real. El cuadro de una bicicleta de carga se enfrenta a fuerzas dinámicas a diario: arranques y frenadas, cargas en curvas, baches e incluso algún que otro vuelco. La resistencia del cuadro a estas fuerzas a lo largo de los años es la verdadera medida de su durabilidad. Gran parte de esto se debe a los factores que hemos analizado (material, diseño, soldaduras, etc.), pero vale la pena examinar específicamente cómo... dinámica de carga y comportamiento del usuario afectan la longevidad del cuadro y cómo los tenemos en cuenta en nuestros diseños.
Cargas dinámicas vs. estáticas: Un chasis puede soportar un peso estático (por ejemplo, una carga útil de 200 kg sin moverla) sin problema. La verdadera prueba es cuando ese peso está en movimiento. Cargas dinámicas incluyen el cambio de peso durante el frenado (cuando frena con fuerza, la inercia de la carga pone fuerza adicional en la parte delantera del cuadro), fuerzas laterales en las curvas (el cuadro puede flexionarse ligeramente hacia los lados bajo un giro brusco) y cargas de impacto verticales (golpear un bache o salirse de un bordillo con una carga introduce un pico de fuerza). Estos eventos dinámicos pueden exceder brevemente el peso estático de la carga. Por ejemplo, una carga de 100 kg que golpea un bache a alta velocidad puede imponer una fuerza efectiva de varias G; momentáneamente, el cuadro se siente como si llevara 200-300 kg en esa sacudida. Un cuadro duradero debe estar diseñado con un margen para absorber estos impactos. Es por eso que simplemente mirar la "capacidad de carga nominal" no es toda la historia; también se trata de los factores de seguridad incorporados. En Regen, simulamos tales eventos con FEA y validamos mediante pruebas de tortura de bicicletas con caídas de peso repentinas y paradas de emergencia. Diseñamos juntas críticas (como la intersección del tubo de dirección y el tubo inferior, y la corona de la horquilla en nuestras bicicletas) para cargas de frenado Muy por encima de lo que se esperaría con un uso normal. Al fin y al cabo, una bicicleta de carga puede pesar fácilmente más de 40 kg. Si sumamos un ciclista (80 kg) y carga (digamos 100 kg), son más de 220 kg moviéndose a alta velocidad. Las fuerzas de frenado sobre el cuadro y la horquilla son enormes. Nos aseguramos de que el tubo de dirección del cuadro y la interfaz de la horquilla soporten estas fuerzas sin doblarse ni agrietarse (además de seleccionar horquillas de alta resistencia adecuadas). Fuerzas de frenado En particular, someten a mucha tensión la parte delantera del cuadro; un cuadro mal diseñado podría agrietarse cerca del tubo de dirección si el material o las soldaduras no son lo suficientemente resistentes. (Nota: esta es una de las razones por las que recomendamos sistemas de frenado potentes, como los discos hidráulicos, en bicicletas de carga. No solo mejora la distancia de frenado, sino que modulan las fuerzas con mayor suavidad. Los frenos mecánicos que se sobrecalientan bajo cargas pesadas pueden debilitarse, obligando a los ciclistas a tirar con más fuerza y potencialmente sobrecargando el cuadro con fuerzas bruscas. La durabilidad del cuadro y el rendimiento de los frenos pueden estar relacionados de esta manera).
Colocación de carga y diseño del bastidor: La ubicación y la forma de colocar la carga pueden influir en la tensión del chasis. Una carga en la caja delantera directamente entre las ruedas tiende a ser más suave con la estructura del chasis (la carga está más centralizada) que el mismo peso colgando de un portaequipajes trasero, lo que genera palanca. Por eso, los diferentes diseños de chasis a veces tienen diferentes capacidades de carga delantera y trasera. Nuestra RS01, por ejemplo, está optimizada para una carga delantera en la caja de carga, colocando el peso cerca del eje de dirección y cerca del suelo. Esto proporciona un mejor manejo y también significa que el chasis no se somete a tanta torsión por una carga oscilante. En nuestros manuales, aconsejamos a los usuarios sobre la carga adecuada (manténgala equilibrada y fíjela para evitar que se mueva). Un chasis resistente resistirá un uso inadecuado, pero las buenas prácticas prolongan su vida útil. Peso y comportamiento del jinete También importa: un ciclista pesado de pie y pedaleando puede ejercer una gran presión sobre la zona del pedalier y las vainas (fuerzas de torsión al balancearse de lado a lado). Esto se tiene en cuenta en las pruebas (prueba de fatiga de pedaleo), pero una conducción agresiva (como saltar bordillos) en una bicicleta de carga completamente cargada, por supuesto, pondrá a prueba los límites de cualquier cuadro. Fabricamos para un uso urbano exigente (por ejemplo, nuestros cuadros tienen un poco más de material en la zona de la horquilla de las vainas para soportar los pares de pedaleo y las sacudidas ocasionales), pero también informamos a los ciclistas de que una conducción suave se traduce en longevidad. Es similar a una camioneta: condúcela dentro de los parámetros normales y durará muchos años; si la sometes constantemente a un maltrato todoterreno, incluso la camioneta más resistente eventualmente necesitará más mantenimiento.
Factores ambientales y de uso: La durabilidad en condiciones reales también se ve afectada por el entorno. Las bicicletas que se utilizan en ciudades costeras con lluvias se enfrentan al problema de la corrosión (que solucionamos con recubrimientos). Las bicicletas que se utilizan en servicios de reparto pueden estar expuestas al sol todo el día, por lo que se utilizan acabados resistentes a los rayos UV para evitar la degradación de la pintura. Los cambios de temperatura pueden provocar que los materiales se expandan o contraigan, lo cual no suele ser un problema para los cuadros metálicos, pero es algo que se debe tener en cuenta para las piezas de plástico. Nuestra filosofía de diseño es considerar... peor escenario posible Un usuario típico podría encontrarse y asegurarse de que el cuadro pueda soportarlo. Por ejemplo, nos preguntamos: ¿qué pasa si la bicicleta se sobrecarga un poco y luego se sube a un bordillo en el frío? Ese escenario combina múltiples factores de estrés. Al probar escenarios compuestos (sobrecarga + impacto en pruebas de laboratorio), buscamos garantizar que ni siquiera eso cause una falla catastrófica. Podría exceder el uso recomendado (y ciertamente no lo recomendamos), pero desarrollar cierta resiliencia forma parte de la ingeniería de durabilidad.
Mantenimiento e inspecciones: Un cuadro resistente también se beneficia de revisiones periódicas. Durante el uso, problemas como el aflojamiento de los tornillos pueden causar problemas secundarios (por ejemplo, el traqueteo de un tornillo suelto puede dañar el soporte del cuadro). Por eso, nuestro Centro de servicio La documentación y el mantenimiento hacen hincapié en la inspección periódica del cuadro y los puntos de fijación. Ofrecemos asesoramiento para detectar desconchones de pintura o manchas de óxido y sus retoques, e inspeccionamos las zonas de soldadura para detectar cualquier signo de grietas o desgaste de la pintura (aunque es extremadamente raro encontrar alguno si se siguen correctamente todos los pasos anteriores). El piloto o el mecánico de la flota desempeñan un papel importante en la detección temprana de problemas. Diseñamos nuestros cuadros para que requieran poco mantenimiento (no existe un "mantenimiento del cuadro" propiamente dicho, salvo mantenerlo limpio y con los retoques necesarios), pero fomentamos una actitud proactiva: si detecta algo, arréglelo antes de que se agrave. Esta combinación de buen diseño y uso responsable garantiza que el cuadro alcance su vida útil prevista.
Historial en el mundo real: Una cosa es hablar de teoría; otra muy distinta es ver que los cuadros siguen funcionando a la perfección después de años. Regen es relativamente joven, pero nuestro equipo cuenta con décadas de experiencia en el sector. Hemos visto nuestros cuadros OEM en condiciones difíciles, desde bicicletas familiares que transportan niños a diario hasta bicicletas eléctricas logísticas que transportan paquetes desde el amanecer hasta el anochecer. La respuesta ha sido muy positiva: nuestros cuadros mantienen la alineación, no presentan grietas ni problemas, y los clientes destacan la sensación de solidez incluso después de un uso prolongado. Nos enorgullecemos de ello, pero nunca descansamos: cada actualización de cuadro es una oportunidad para mejorar aún más la durabilidad, a menudo incorporando pequeñas mejoras obtenidas de datos de campo.
Al final, el cuadro de una bicicleta de carga soporta una vida dura en el mundo. Al comprender las fuerzas y comportamientos del mundo real, y diseñar y probar en consecuencia, garantizamos que nuestros cuadros, y por extensión, sus bicicletas, puedan soportar el desgaste diario año tras año. Se trata de... resistencia estructuralNo solo sobreviviendo a una sola prueba, sino prosperando en innumerables entregas, viajes familiares o aventuras. Ese es el verdadero sello de la durabilidad.
Conclusión
La durabilidad del cuadro de una bicicleta de carga se debe a una sinergia de factores. Comienza con selección inteligente de materiales (utilizando el metal adecuado para el trabajo y tratándolo adecuadamente), fluye hacia Geometría bien pensada y diseño de unión robusto (para que las cargas queden bien distribuidas), está garantizado por Soldadura de alta calidad y fabricación de precisión (eliminando eslabones débiles), y está comprobado a través de Pruebas rigurosas y validación en el mundo real (para que ninguna suposición quede sin comprobar). Añadiendo capas de protección contra la corrosión preserva esa fuerza a largo plazo y la comprensión uso en el mundo real Guía tanto nuestro diseño como la educación de nuestros usuarios para que esos cuadros sigan funcionando con fuerza.
Desde nuestra perspectiva en primera persona en Regen, donde diseñamos, construimos y ensamblamos cuadros de bicicletas de carga a diario, enfatizamos que la durabilidad no es casualidad, sino ingeniería. Cada decisión, desde la elección del aluminio 6061-T6 y su recubrimiento ED, hasta el refuerzo del tubo de dirección y la alineación milimétrica de cada puntera, contribuye a un cuadro en el que puede confiar su sustento (o la seguridad de su familia). Como fabricantes de equipos originales (OEM/ODM) de bicicletas de carga, nuestra reputación depende de estos cuadros tanto como la de nuestros clientes. Por eso, invertimos en durabilidad en cada paso del proceso y colaboramos con expertos a nivel mundial (en China para una fabricación eficiente, en Portugal para un ensamblaje y control de calidad de primera calidad) para ofrecer lo mejor de ambos mundos.
En la práctica, ¿qué significa esto para ti, lector? Si marcas bicicletas de carga, puedes personalizar tu próximo modelo con confianza, sabiendo que la plataforma es sólida, y estamos aquí para ayudarte como tu socio de soluciones. Si eres conductor o operador de flota, significa tranquilidad: un cuadro de bicicleta de carga bien construido. Podría ser la menor de tus preocupaciones Incluso al llevarlo al límite. Y si solo siente curiosidad, esperamos que haya comprendido el rigor de ingeniería que se aplica a esa humilde estructura tubular que transporta sus compras o paquetes.
La resistencia y durabilidad de un cuadro no son mágicas; son el resultado del conocimiento, el esfuerzo y la calidad. En Regen, hablamos de estos temas con pasión porque, literalmente, nuestro trabajo es fabricar bicicletas duraderas. Esperamos que este análisis profundo haya desmitificado el tema y mostrado por qué se toman ciertas decisiones en la industria. Un cuadro de bicicleta de carga debe resistir mucho, pero con el enfoque adecuado, puede hacerlo con elegancia y fiabilidad. ¡Brindemos por fabricar bicicletas que resistan el paso del tiempo (y las cargas pesadas)!
Referencias
- Ingeniería Hambini. (2023). Normas de fabricación de cuadros de bicicletas. (Información sobre la producción de cuadros OEM y la importancia del control de calidad para garantizar la fiabilidad)
- Serfas. (sin fecha). Materiales del cuadro de la bicicleta: conozca las diferencias. (Descripción general de las características del aluminio, acero, titanio y carbono; señala que los marcos de aluminio se fatigan más rápidamente, mientras que el acero es altamente resistente a la fatiga)
- Singh, G. (sin fecha). 1000 horas de resistencia a la niebla salina en herrajes – Foro de Finishing.com. (Comentario de un experto de la industria que señala que el recubrimiento electrolítico catódico cumple con más de 1000 horas de prueba de niebla salina ASTM B117 sin óxido rojo)
- Bicicletas Tern. (sin fecha). Cómo probamos la seguridad de nuestras bicicletas de carga y transporte de pasajeros. (Protocolo de pruebas de Tern para cuadros de bicicletas de carga, que incluye métodos internos de "prueba hasta el fallo" y supera los estándares DIN 79010)
- Vello Bikes. (23 de octubre de 2023). VELLO SUB establece nuevos estándares con EFBE-TRI-TEST®. (Anuncio de que la bicicleta de carga pasa la prueba EFBE Tri-Test; explica las pruebas de fatiga y sobrecarga de 100.000 ciclos de Tri-Test para cuadros)