Chytřejší způsob připojení baterií, senzorů a dalších zařízení
Úvod: Proč je digitální komunikace v moderních elektrokolech důležitá?
Jako Regen, jsme odhodláni konstruovat nákladní elektrokola, která nejen dobře jezdí - ale také think dobře. S tím, jak se naše kola vyvíjejí a zahrnují inteligentní displeje, přesné snímače točivého momentu, sledování GPS, připojení k internetu věcí a systémy správy baterií (BMS), je potřeba robustního komunikačního protokolu nepopiratelná.
Zde je Sběrnice CAN vstupuje do hry.
Sběrnice CAN (Controller Area Network) je digitální komunikační protokol, který umožňuje všem klíčovým elektronickým součástem elektrokola - řídicí jednotce, baterii, displeji, motoru a senzorům - komunikovat více než jen pomocí kabeláže. vzájemně komunikovat prostřednictvím sdílené sítě. V tomto článku vysvětlíme:
- Co je sběrnice CAN
- Srovnání s UART
- Proč je pro moderní elektrokola nezbytná, a to zejména pro nákladní kola
- Aplikace v reálném světě a úvahy o integraci
- Výhody, nevýhody a výhled do budoucna
Co jsou komunikační protokoly v elektrických systémech elektrokol? Kliknutím sem získáte komplexního průvodce
Co je sběrnice CAN? (Controller Area Network)
Stručná definice
Sběrnice CAN (Controller Area Network) je protokol založený na zprávách s více správci, který byl původně navržen pro aplikace v automobilovém průmyslu. Umožňuje více elektronických řídicích jednotek (ECU) komunikovat prostřednictvím jediného páru kroucených vodičů bez potřeby centrálního počítače.
V kontextu elektrokol mohou tyto řídicí jednotky zahrnovat:
Zařízení | Role |
---|---|
BMS baterie | Monitorování nabíjení/vybíjení, teploty, stavu |
Řídicí jednotka motoru | Provádí logiku asistence při sešlápnutí pedálu, odezvu na plyn. |
Zobrazovací jednotka | Rozhraní s jezdcem; zobrazuje rychlost, dojezd, chybové kódy |
Senzory (točivý moment, otáčky) | Podávání vstupů v reálném čase pro řízení asistence motoru |
Jednotka GPS/IoT (pokud je k dispozici) | Poskytuje lokalizaci, diagnostiku, správu vozového parku |
Namísto vedení jednotlivých vodičů mezi jednotlivými zařízeními (jako v případě analogových konfigurací nebo konfigurací UART) umožňuje sběrnice CAN. všechny komponenty sdílejí stejnou datovou linku, což snižuje složitost a zvyšuje spolehlivost.
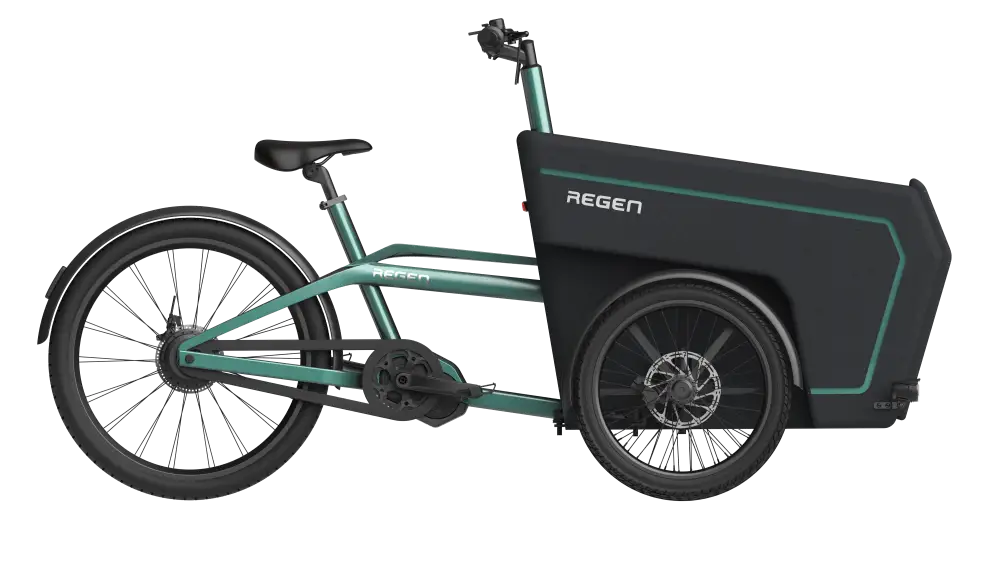
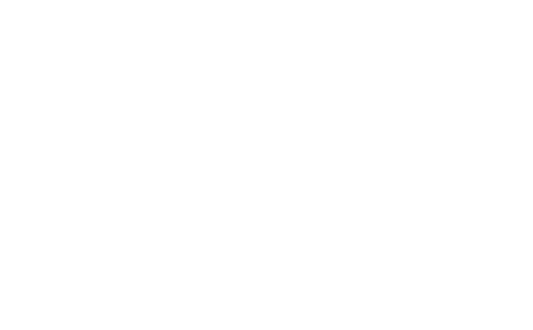
Pouze 20 minimálních objednávkových kol pro začátek
Přizpůsobitelné nákladní elektrokolo - RS01
Ať už jste rostoucí značka nebo místní obchod, naše těžká nákladní kola jsou vaší vstupenkou do prosperujícího světa ekologického doručování. Pojďme na to!
UART vs. sběrnice CAN: jaký je mezi nimi rozdíl?
UART (univerzální asynchronní přijímač a vysílač) je dalším oblíbeným protokolem v systémech elektronických kol. Je jednodušší a levnější, ale jeho rozsah je omezenější.
Zde je jejich srovnání:
Funkce | UART | Sběrnice CAN |
---|---|---|
Typ komunikace | Bod-bod (1:1) | Síť s více uzly (mnoho:mnoho) |
Detekce chyb | Základní (paritní bity) | Robustní (CRC, ACK, opakování) |
Složitost kabelů | Více drátů na zařízení | 2vodičová sdílená sběrnice |
Škálovatelnost | Omezené | Vysoká - snadné přidání dalších uzlů |
Rychlost | Obvykle pomalejší (9600-115200 bps) | Rychlejší (až 1 Mb/s) |
Případ použití | Základní elektrokola | Pokročilá/nákladní elektrokola, flotilové systémy |
Regen Insight: Většina příměstských elektrokol základní úrovně stále používá UART. Ale u našich modulárních nákladních kol - kde jsou běžné moduly IoT, duální baterie, rekuperační brzdění a více senzorů - je to mnohem jednodušší. Sběrnice CAN je jediným škálovatelným řešením.
Proč je sběrnice CAN ideální pro nákladní elektrokola
Nákladní kola nejsou jen nadměrná jízdní kola - jsou to chytré dopravní stroje, které jsou často určeny pro. logistika, rodinná mobilita nebo komerční flotily.. Tyto případy použití vyžadují:
- Řízení krouticího momentu v reálném čase pro velká zatížení
- Monitorování stavu baterie pro dvě balení
- Sledování GPS a upozornění na krádež
- Integrace s aplikacemi pro doručování nebo systémy pro správu vozového parku
- Prediktivní údržba a zaznamenávání chyb
To vše vyžaduje stabilní, vysoce výkonná komunikace mezi moduly - přesně to sběrnice CAN nabízí.
Příklad aplikace: Nákladní elektrokolo pro flotilu
Představte si flotilu nákladních kol Regen, která používá poštovní společnost:
- Ten/Ta/To zobrazit zobrazuje jezdci diagnostiku v reálném čase.
- Ten/Ta/To BMS baterie odesílá údaje o stavu nabití a teplotě, aby se zabránilo přetížení.
- A Jednotka GPS zaznamenává polohu a pomáhá s optimalizací trasy.
- Ten/Ta/To řídicí jednotka upravuje výkon na základě užitečného zatížení, terénu a zpětné vazby od senzorů.
Díky sběrnici CAN Bus sdílejí všechny tyto komponenty data na jedné jednotné páteři - s minimální latencí a maximální koordinací.
Schéma architektury systému
Zde je zjednodušená vizualizace systému elektrokol na bázi sběrnice CAN:
+------------------+
| Zobrazovací jednotka |
+------------------+
|
+-------------+--------+---------+--------------+
| | | |
+--------+ +----------+ +---------+ +-----------+
| Senzor | Baterie | Motor | GPS/IoT |
| (např. | | BMS | Ctrl. | Modul |
| točivý moment)| +----------+ +---------+ +-----------+
\___________________________________________/
Sdílená sběrnice CAN (kroucená dvojlinka)
Tato architektura výrazně snižuje nepořádek v kabeláži a zvyšuje modularitu - usnadňuje opravy, modernizace nebo diagnostiku.
Výhody sběrnice CAN v elektrokolech
Benefit | Proč na tom záleží |
---|---|
Modularita | Snadné přidávání/odebírání komponent (např. nových senzorů) |
Diagnostika | Čtení chybových kódů, vzdálený záznam problémů |
Škálovatelnost | Vhodné pro komplexní systémy a velké flotily |
Bezpečnost | Zabraňte přepětí, přehřátí, spuštění plynu |
Protokolování dat | Umožňuje prediktivní údržbu a analýzu vozového parku |
Zkrácená elektroinstalace | Zjednodušuje konstrukci rámu a zlepšuje vodotěsnost |
Dodržování norem
Moderní systémy sběrnice CAN v elektrokolech jsou stále více sladěny s bezpečnostní normy pro automobilový průmysl, jako např:
- ISO 11898 (standard protokolu CAN)
- EN 15194 (norma EU pro EPAC včetně elektrické bezpečnosti)
- EN 50604-1 (Komunikace a ochrana BMS baterie)
Systémy Regen navrhujeme s ohledem na tyto standardy, abychom zajistili. Dodržování předpisů na trhu EU a dlouhodobá spolehlivost.
Nevýhody a omezení
Sběrnice CAN Bus sice nabízí přesvědčivé výhody, ale není bez kompromisů:
Omezení | Vysvětlení |
---|---|
Vyšší náklady | Složitější mikrokontroléry a kódování |
Doba vývoje | Vyžaduje integraci a testování firmwaru ve všech zařízeních. |
Kompatibilita součástí | Všechny moduly musí používat stejné protokoly CAN (např. CiA 454 nebo vlastní). |
Obtížnost opravy | Diagnostika závad může vyžadovat specializované nástroje nebo software. |
Tyto nevýhody však do značné míry převažují. výhody v profesionálních aplikacích nebo aplikacích na úrovni vozového parku.
Sběrnice CAN v ekosystému nákladních elektrokol Regen
Ve společnosti Regen integrujeme sběrnicové systémy CAN do našich platformy pro nákladní kola střední a vyšší třídy, zejména když:
- Zákazníci vyžadují sestavy s více bateriemi
- Kolo obsahuje správa vozového parku nebo IoT integrace
- Případ použití zahrnuje těžký náklad, časté cykly zastavení a rozjezdu.nebo náročný terén
Podporujeme také hybridní systémy - kombinace UART (pro starší zobrazovací jednotky) a CAN (pro pokročilé moduly) - s Mosty CAN aby byla zajištěna budoucí kompatibilita a bezproblémové upgrady.
Jak zjistit, zda elektrokolo používá sběrnici CAN?
Zde jsou tři vodítka:
- Méně kabelů propojení hlavních komponent (často pouze dvouvodičová sběrnice).
- Displej umožňuje diagnostiku celého systému (nejen chyba motoru).
- Podpěry pro jízdní kola aktualizace firmwaru nebo monitorování na úrovni aplikací ve více modulech.
Ve společnosti Regen pomáháme zákazníkům OEM a ODM navrhnout vlastní komunikační architekturu aby vyhovovaly jejich plánu produktů a rozpočtu - od jednoduchých UART až po chytrá kola s plnou sběrnicí CAN.
Závěr: Chytřejší připojení pro chytřejší kola
Sběrnice CAN je víc než jen datový kabel - je to základ pro inteligentní a propojená elektrokola. Pro rodinné jezdce, kteří chtějí mít klid, a pro provozovatele logistiky, kteří vyžadují provozní efektivitu, Nákladní kola se sběrnicí CAN nabízejí bezkonkurenční ovládání, diagnostiku a možnost modernizace..
Ve společnosti Regen podporujeme značky při budování elektrická nákladní kola připravená na budoucnost prostřednictvím flexibilního návrhu systému, který je v souladu s normami. Pokud navrhujete novou platformu nebo přecházíte z UART na CAN, pojďme si promluvit - náš tým inženýrů je připraven vám pomoci od specifikace až po rozšíření.
📩 Kontaktujte nás a prozkoumejte řešení sběrnice CAN pro svůj projekt nákladního kola.